How industrial companies are mastering the digital transformation: five essential steps
8. November 2023- digital transformation
- smart factory
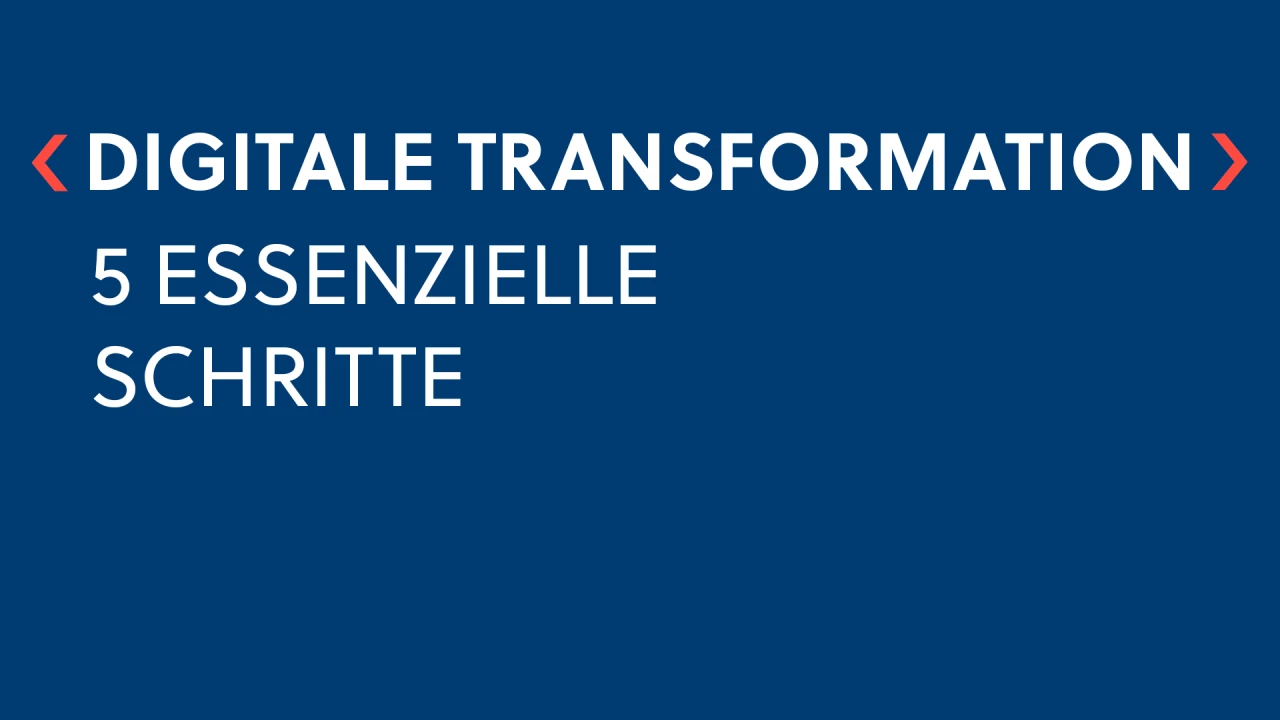
Industrial companies face significant challenges due to political, structural and organizational hurdles. To ensure their competitiveness and future viability, these companies must initiate a holistic transformation of their operations.
“For many decision-makers, the variety of topics and technologies associated with buzzwords such as digital transformation, smart factory or Industry 4.0 is a challenge,” emphasizes Thomas Rohrbach, Managing Director and co-founder of NEONEX. In order to lead industrial companies on a successful path to the digital transformation of their operations, he explains five key steps that companies should consider:
1. Create a common vision and standardized vocabulary
At the start of the digital transformation, companies should develop a shared vision and a target image for their smart factory that is derived from the company's objectives. This target image describes which characteristics a smart factory must develop in order to support competitiveness and ensures a shared awareness of the problem. To further support the change process, companies should also ensure that all stakeholders use the same vocabulary. This prevents misunderstandings and promotes coherent communication.
2. Identify and evaluate optimization potential
In the next step, companies should identify all potential for improvement along the value stream in production, logistics and business processes. The involvement of all employees is crucial here. After identification, the identified digitalization, automation, analytics and lean potentials are jointly evaluated and transferred to a roadmap. Clear prioritization is particularly important here to ensure focused implementation.
3. Define IT architecture and use cases
The development of the IT architecture is an essential step in the transformation initiative. Companies must ensure that the IT strategy is aligned with the planned use cases and that the requirements for data usage and data networking are defined. Monolithic systems such as manufacturing execution systems (MES) offer a standardized solution for production and logistics with fully integrated data models. Low or no-code platforms can also be used to develop smaller use cases more quickly. The IT architecture should be flexible enough to support future requirements.
4. Agile project management and effective communication
Agile project management is the best way to successfully implement the digital transformation. Iterative sprints make it possible to react flexibly to changes and maintain the speed of the transformation. A well thought-out communication strategy also ensures that all stakeholders are continuously informed and involved. This includes the development of a showcase, the consistent use of internal communication channels and regular mutual updates.
5. Ensure roll-out and continuous improvement
The success of a digital transformation is achieved when all use cases are fully rolled out and the synergies between different plants and departments within the production system become clear. It is crucial to develop pilot use cases to ready-to-deploy status and map them through a dedicated roll-out team that has the appropriate resources. The continuous improvement process should be ensured through ongoing review and adaptation as well as feedback loops.
These structured steps offer valuable guidance for a successful digital transformation. Practical examples show the positive results of successful digitalization projects: Real-time transparency across the entire production process, significant reduction of manual tasks, increased flexibility, enhanced customer focus, more efficient processes and higher customer satisfaction as well as data-based decision-making. Corresponding results emphasize the importance of a well thought-out and targeted initiative.
About NEONEX
NEONEX supports industrial companies in the digital transformation of their operations. The management consultancy was founded in Stuttgart in 2017 by Thomas Rohrbach, Dr. Jochen Schlick and Dr. Peter Stephan. The company develops and implements customized strategies for production and the supply chain. Customers benefit from the intelligent combination of people, technologies and processes. The Stuttgart-based company has 28 employees in Europe, America and Asia and has won several awards.