HOMAG
Datengetriebene Montageoptimierung mit Virtual Cardboard Engineering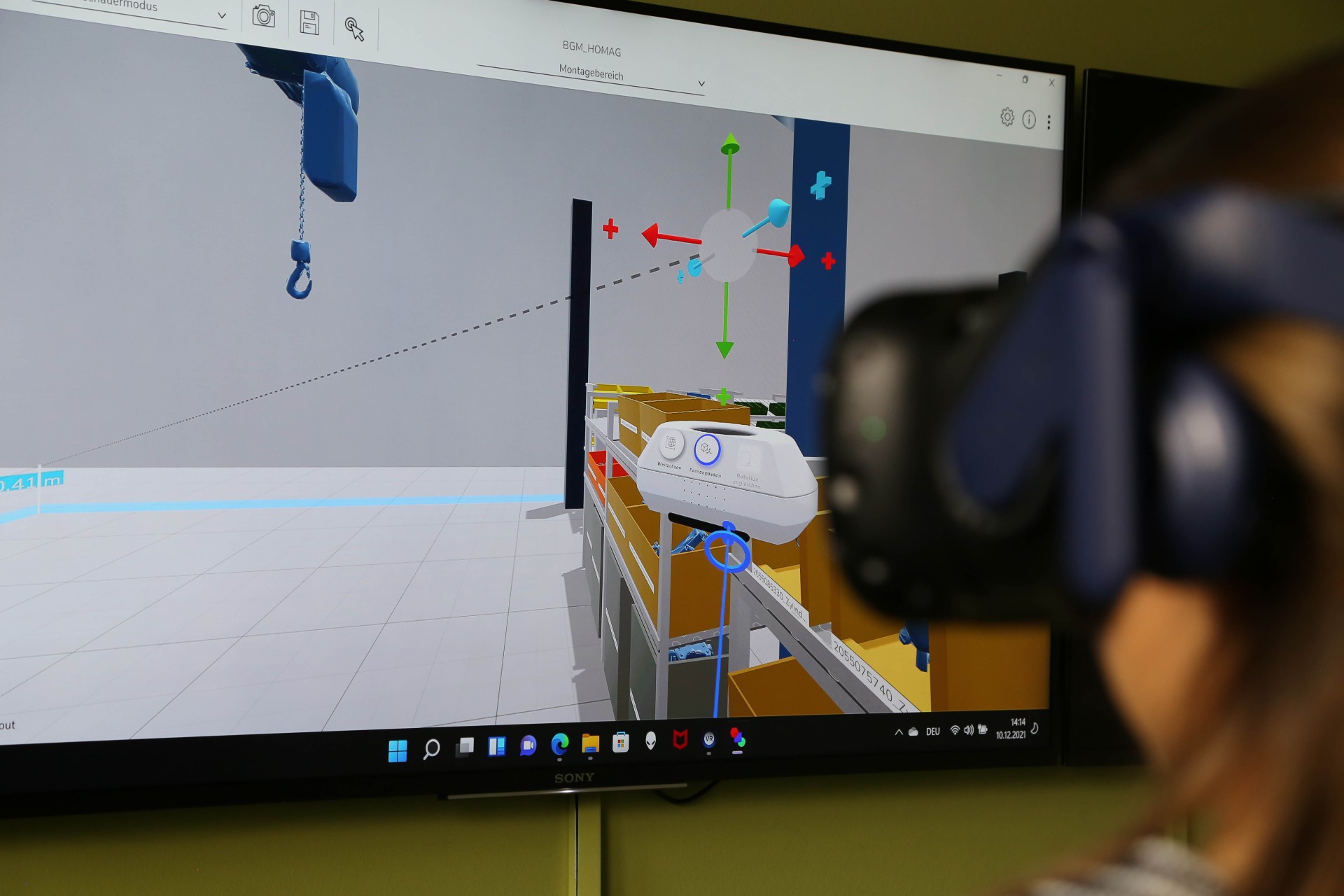
Das Ziel des Projektes bei der HOMAG war es, schnellere Auftragsdurchlaufzeiten, eine höhere Flexibilität über die unterschiedlichen Typen und die Glättung von Auftragsspitzen in der Montage zu erreichen, um die Kunden des Herstellers von Produktionslösungen für die holzbearbeitende Industrie noch schneller beliefern zu können.
Bisher wurden die unterschiedlichen Aggregattypen der HOMAG auf speziell dafür vorgesehenen Arbeitsplätzen montiert, so dass die Ausbringungsmenge limitiert und die Planung bei Schwankungen in der Produktnachfrage komplizierter gestaltet wurde.
Um dies zu optimieren, startete das Team aus Mitarbeitern und Beratern von NEONEX mit der Aufnahme der IST-Situation durch Eindrücke vor Ort und die datenbasierte Auswertung der bisherigen Montageprozesse.
Anschließend erfolgte die Auslegung des neuen Systems auf Basis der geplanten Ausbringungsmenge, mit der Möglichkeit, weiteres Wachstum abbilden zu können. Das Team aus Mitarbeitern der HOMAG und den Berater*innen von NEONEX entwickelte so ein Idealbild, welches Schritt für Schritt in ein Realbild umgesetzt werden sollte.
Durch den konsequenten Einsatz von VR bei der Gestaltung des Arbeitssystems konnte in einer geringen Zeit ein komplettes System von ca. 400 m² Montagefläche mit einem hohen Detailierungsgrad entwickelt werden. Statt wie im klassischen Cardboard Engineering die Arbeitsstationen aus Pappe zu bilden, werden im Virtual Cardboard Engineering die Arbeitsstationen mit Hilfe von VR-Brillen in der virtuellen digitalen Realität konstruiert.
Dies hat mehrere Vorteile: zum einen ist dieser Ansatz ressourcensparender, besonders flächeneffizient und kann, wenn die Umstände dies erfordern, auch remote durchgeführt werden. Zum anderen können existierende 3D Modelle in das VR-Modell eingebunden werden, so dass die virtuelle Realität greifbar wird und Projektmitarbeiter und Berater sich besser in das Modell hineindenken, hierbei eventuelle Störungen identifizieren und direkt beheben können.
Dieser Umstand erleichtert außerdem die Akzeptanz des Systems, da auch die Mitarbeiter auf dem Shopfloor das Modell ansehen und ihren wichtigen Input liefern können. So können die Mitarbeiter schneller und stärker eingebunden werden und deren Akzeptanz für die Veränderungen steigt.
Auf Basis des finalen Layouts war die HOMAG in der Lage, die Montagesysteme vollumfänglich einzukaufen und das neue Layout anhand des VR-Modells umzusetzen. Die Berater von NEONEX brachten dabei zum einen ihre langjährige Expertise hinsichtlich schlanker Montagesysteme / Prozesse ein und übernahmen zu anderen das agile Management des Projekts.
Das Ergebnis des Projektes ist ein zukunftsweisendes Montagesystem, welches in abgewandelten Formen in der gesamten Unternehmensgruppe angewendet werden kann.
In diesem System kann ein hochflexibler Modellmix ohne Restriktionen montiert werden. Die Mitarbeiter der HOMAG konnten dabei im Laufe des gesamten Projektes ihren Input liefern und so gemeinsam mit NEONEX das neue System entwickeln, das eine Produktivitätssteigerung von mind. 20% und ein atmendes System für die HOMAG bedeutet.
Der Nutzen für HOMAG
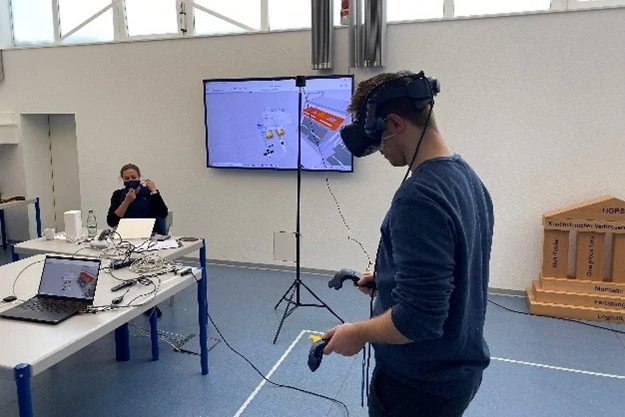