HOMAG
Data-driven assembly optimization with Virtual Cardboard Engineering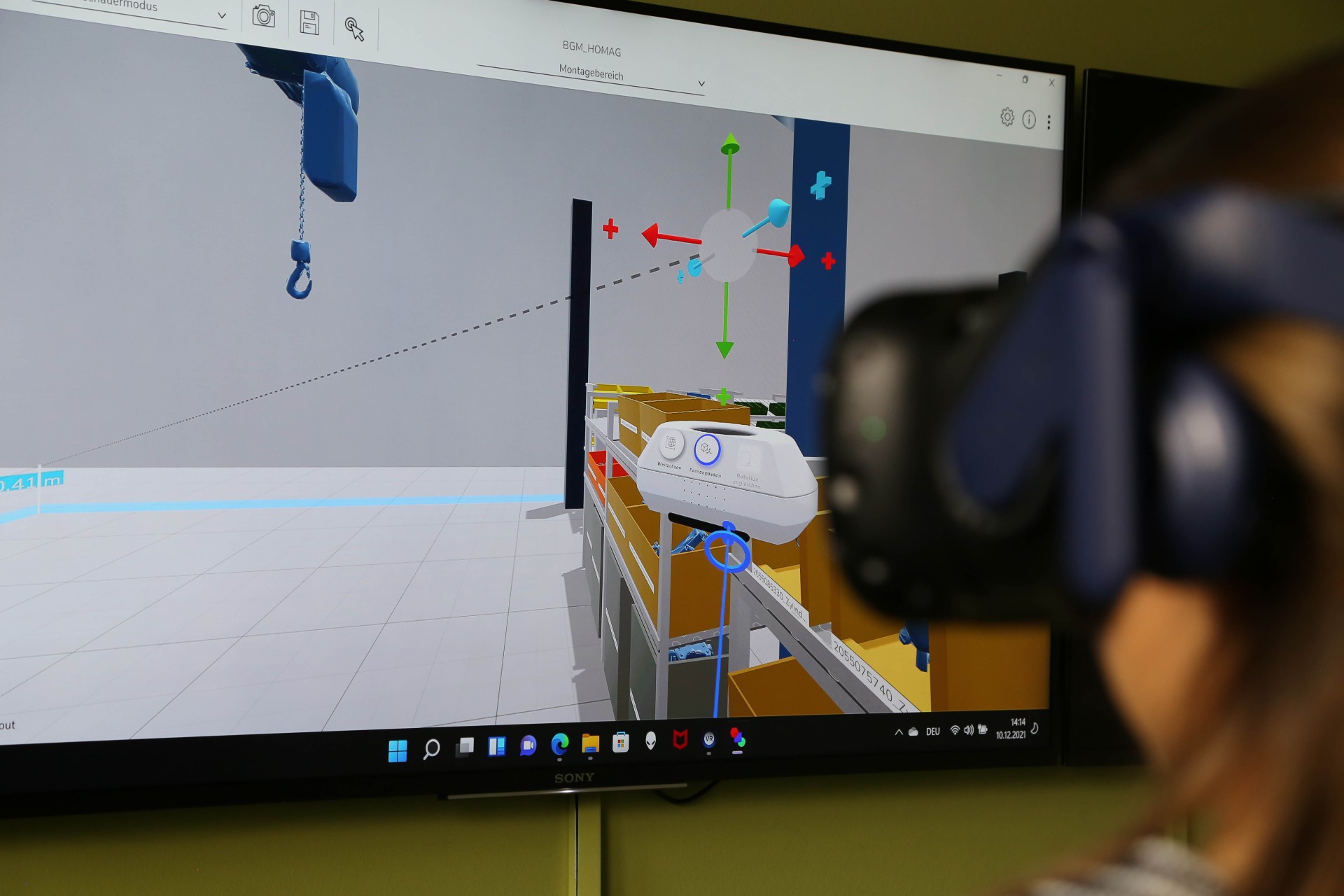
The goal of the project at HOMAG was to achieve faster order throughput times, greater flexibility across the different types and the smoothing of order peaks in assembly in order to be able to supply the customers of the manufacturer of production solutions for the woodworking industry even more quickly.
Previously, HOMAG's different aggregate types were assembled at specially designated workstations, limiting output and complicating planning in the event of fluctuations in product demand.
In order to optimize this, the team of employees and consultants from NEONEX started with the recording of the current situation through impressions on site and the data-based evaluation of the previous assembly processes.
Subsequently, the design of the new system was based on the planned output quantity, with the possibility of being able to map further growth. The team of HOMAG employees and NEONEX consultants thus developed an ideal image, which was to be converted step by step into a real image.
Through the consistent use of VR in the design of the work system, it was possible to develop a complete system of approx. 400 m² assembly area with a high level of detail in a short period of time. Instead of forming the workstations out of cardboard as in classic Cardboard Engineering, in Virtual Cardboard Engineering the workstations are constructed in virtual digital reality with the help of VR goggles.
This has several advantages: on the one hand, this approach is more resource-efficient, particularly space-efficient, and can also be carried out remotely if circumstances require. On the other hand, existing 3D models can be integrated into the VR model, so that virtual reality becomes tangible and both project staff and consultants are better able to think their way into the model, identify any faults in the process and rectify them directly.
This circumstance also facilitates the acceptance of the system, as employees on the store floor can also view the model and provide their important input. In this way, employees can be involved more quickly and to a greater extent, and their acceptance of the changes increases.
Based on the final layout, HOMAG was able to fully purchase the assembly systems and implement the new layout using the VR model. The consultants from NEONEX contributed their many years of expertise regarding lean assembly systems / processes on the one hand and took over the agile management of the project on the other hand.
**The result of the project is a future-oriented assembly system, which can be used in modified forms throughout the entire group of companies.
In this system, a highly flexible model mix can be assembled without restrictions. HOMAG's employees were able to provide their input throughout the project and thus develop the new system together with NEONEX, which means a productivity increase of at least 20% and a breathing system for HOMAG.
The benefits for HOMAG
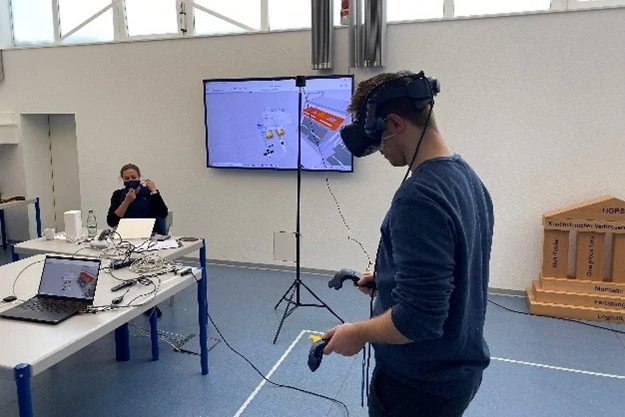