Getting things done while implementing MES
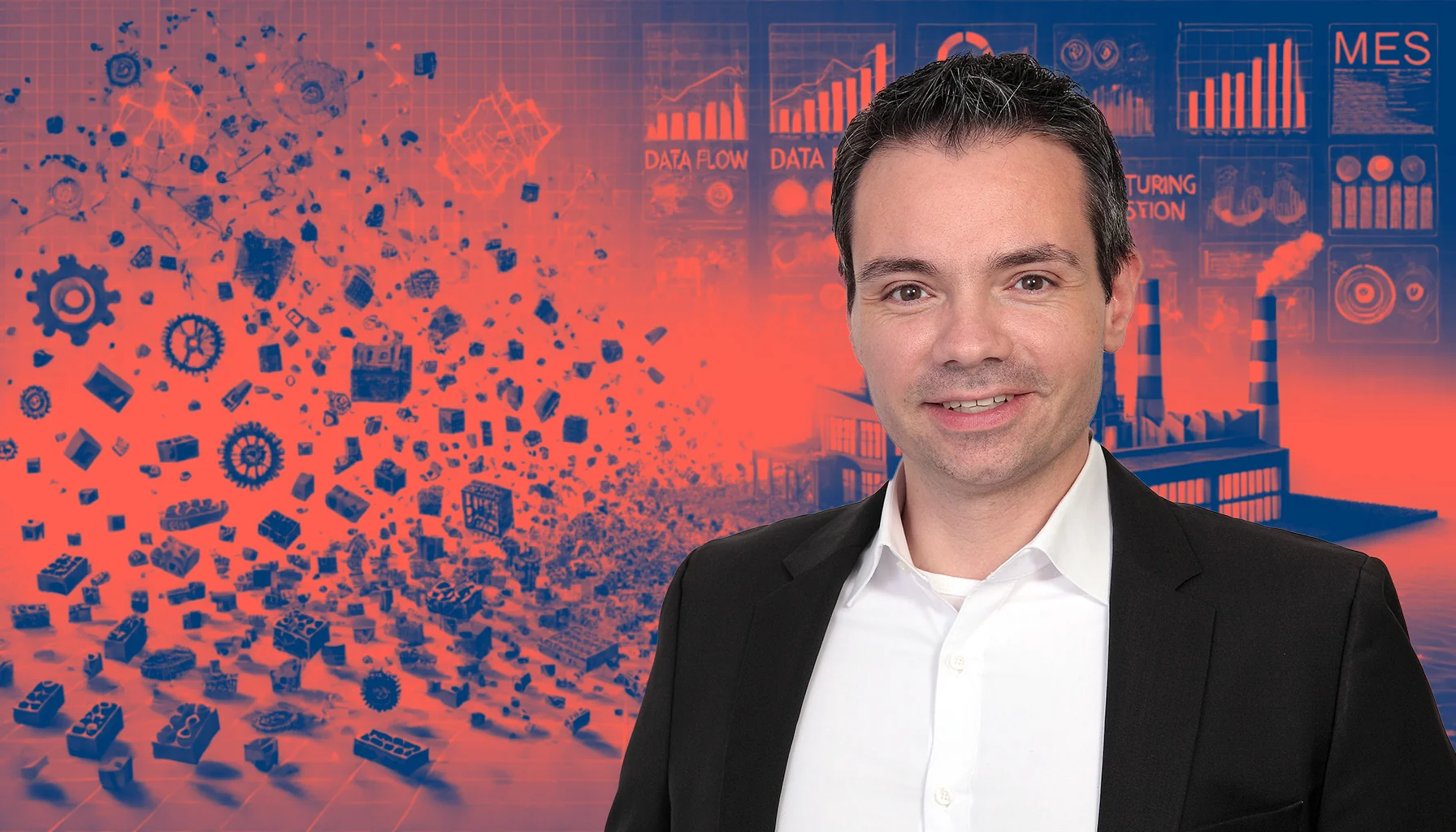
Selecting the right Manufacturing Execution System (MES) is already a tricky story. But it’s easily forgotten that the real work is only starting right after.
Implementing Manufacturing Execution Systems (MES) is nothing like running a windows update. Both technology and processes as well as organization need to be taken into account. But don’t worry, it’s not a sealed book and can be broken down into some major Do’s & Don’ts that will keep you safe from the biggest trouble. In the following article, we highlight the top ten factors to make an MES implementation run as smoothly as possible.
Don’t underestimate project management, it’s key!
Project management (PM) is by far the most underestimated factor for a successful MES implementation. Related budgets are the first to be cut and the task is often assigned to someone who is already occupied by other demanding duties. If you do not want to go for the hazards of such an approach, be advised to do better.
The NEONEX best practice to run a MES implementation smoothly is to go for a hybrid PM-approach, which means to work with clear milestones but with methods from agile toolboxes to monitor progress closely and to immediately react on deviations when they occur. That means, running sprint plannings on a weekly basis, holding daily check-ins & check-outs for the most critical tasks and going for steering committees in a monthly rhythm, in order not to lose the bird’s eye view. In addition to that, it is key to keep hierarchies flat and empower teams and people to make decisions on the low level of the pyramid in order to ensure pace and not getting stuck in the mud. And for god's sake, give the overall project management responsibility to a skilled person with some experience with MES. If you do not have one, go for some external support. It will pay off multiple times.
Go for small bits & bites to get traction and keep the pace!
When it comes down to listing tasks and to-do’s, writing user stories is a means of choice in software projects. Typical mistakes are quite often made with tasks described not granular enough to get closed during a single sprint. This leads to the situation that to-do’s are rotting for weeks in the SCRUM board without making visible progress and without having a glance about their actual status.
NEONEX best practice to create appropriate user stories is to capture ALL tasks to be performed to get MES running, not only the software implementation related ones. There is much more to do regarding preparation of master data in the backend and infrastructure on the shop floor to get assets online. List them all to keep a transparent overview! Secondly, it’s the granularity that matters most. Making sure that defined work items are small enough to get done in a single sprint is crucial to have transparency about status and progress as well as keeping the team motivation at a good level.
Get your master data clean and complete!
Being in the woes of technical MES integration, it is easily forgotten that empty systems do not support operations in any way. Besides working interfaces and clearly defined processes, correct and complete master data is the ingredient to bring MES to life. NEONEX best practice is to take care of master data correctness and completeness early in the process. Thinking of master data is a wide field. Starting with material master data, BOMs, workplans, shift models and staff qualification levels, also all kinds of planned process times are to be prepared. When digging deep, keep in mind that it is not the goal to go for 100% accuracy in every detail. Try to reach a decent level of quality for the high runner products with the largest sales volumes. The rest can be updated later. When preparing master data, it is key to have migration in mind. Considering tools for automated or semi-automated migration is a must, not to drown in the mass of data to be handled.
Take a close look at all the Excel stuff!
In lots of companies dealing with high mix low volume product portfolios, there are logic relations existing to match process parameters, required special treatments or legal regulatory documents with the actual product variant produced. Typically, this is done by product characteristics being specified by engineering. Such kinds of matching logics typically exist in well-kept excel sheets created by industrial engineering experts helping to handle the complexity implied by serving the market with your complete product portfolio.
In order not to lose this cornerstone of your daily operations it is NEONEX Best practice to get your IE-experts involved in the MES core team early in the process. Check where such logics are reflected best. Relations and structures can easily get complex, and product characteristics may be defined in different steps of your order fulfilment process. No matter if it is in your sales configurator, ERP or MES, make sure that such logic relations are migrated correctly, to avoid a bad awakening when turning the keys of the new system.
For the target process design, get the dirty hands to the table!
It is clear to most people that the definition of standard processes is a key task to do when implementing MES. But often it seems that only a few have an idea on how to do it right. “Right” in this context means to define processes that will be widely accepted and complied by daily users. It is quite often the comfortable workaround to make use of already existing process templates of the MES supplier, add some good improvement ideas from the management and get things implemented before talking to the staff who actually run the daily business. This often results in serious amounts of frustration or even in refusing the implemented solution at all.
To avoid these extremely expensive mistakes, it is NEONEX best practice to bring people from the shopfloor as early as possible to the table. May it be some team or shift leader or even ordinary workers with 10+ years of experience. Those people know how to get daily work done and where waste is created in the status quo. In this stage the only important management contribution is to ensure that improvement potentials are focused, and MES capabilities are leveraged best. The design of the processes is then a job that will be done best by the guys getting their hands dirty on a daily basis.
Decide on how to control your operations!
To make the best use of an MES, you must decide on how to control operations in your company. If this is not clarified prior to MES implementation, it is quite likely that you will have an up-and-running system after the pains of go-live and hyper care, but that actual benefits of MES cannot be measured or even felt at all. If so, disappointment and frustration kick in hard, after having spent time, money and effort. The NEONEX best practice approach to avoid going through this “valley of disappointment” is about implementing the right KPI and decision making processes on the right level of insight. To achieve that, it make sense to think about the three main levels to control operations and making decisions:
- Live monitoring
Monitoring actual processes in the scale of seconds to minutes to get aware of deviations and to decide on counter measures immediately. Typically, those live monitoring applications are realized in MES. Good examples are dashboards to check plan vs. actual figures of materials, components and products produced. - Manufacturing analytics
Weekly or monthly standard reporting allow manufacturers to identify waste and deficits to be solved sustainably in PDCA (Plan Do Check Act) cycles. Also, this kind of standard reporting is a typical MES functionality. Good examples are improving KPI’s like MTTR (Mean time to repair) and MTBF (Mean time between failures) to increase efficiency and effectiveness of maintenance teams. - Advanced analytics
Complex statistical analysis with advanced mathematical approaches to solve problems with non-obvious root causes, requiring processing of large amounts of data. This kind of analytics is realized by applying business intelligence functionality, accessing data stored in large scale historian databases. Such functionality and backend infrastructure are typically not standard for MES. Good examples are the analysis of quality problems in thermoforming processes based on 200 something influential parameters.
Defining KPI and visualizations precisely on those three levels will help to align business requirements with technical realization platforms early in the process. Following such an approach ensures that the capabilities of MES unfold their full potential and put you in the driver seat to run your operations.
Assign the right guys the job of key user and process owner!
Another underestimated aspect of MES implementation is the assignment of the right roles to the right people. Besides the core team for technological and operational MES implementation, you need to assign two major roles to get the entire organization working in MES:
- Key user, who will be the main multiplier of MES application-know-how at the frontline of daily operations on the shopfloor
- Process owner, who has the responsibility to govern the correct implementation and also multiplication of their processes on a global scale during each and every roll out.
To get a good start, NEONEX best practice is about putting some brain capacity to assign the right people to the right job.
For the role of key user, you need characters who are into technology and system interaction, but also good communicators. Being key user is about spreading the word and helping the average user to get along with the new stuff. So, you do not need the brilliant eggheads, but more of the smart socializers who are into supporting others and sharing what they know.
For the role of process owner, you are better off with characters that are deep into operations process of their responsibility and who love to set and keep standards. As this might be pain-in-the-ass for all locals in following roll out plants, you need such characters to keep order and to set a good baseline for a global MES installation. Good process owners ensure that the potential of MES to force process excellence and to provide comparability of performance in more than one plant will materialize.
Plan go-life & hyper care with enough time and resources!
When implementing an MES, there is a point in time when you actually turn the key, and everyone has to live in the new system. You are either coming from an existing legacy implementation and need to take care of a meticulously planned migration, or you start from zero and staff need to deal with processes that do not allow manual workarounds of a paper-based world anymore. In both cases the go-live and the first weeks after remain hard to imagine for everyone who has not yet gone through.
To avoid a rude awakening, NEONEX best practice is to do thorough preparation with your team and all external parties involved. Cornerstone of this preparation is a plan for at least 2-3 days in the granularity of hours. This is the only chance to synchronize the manifold activities as required to realize a transition as smoothly as possible.
For hypercare phase, it is NEONEX best practice to plan support for at least 2 months, not to leave your operations staff alone with a new system. Be generous with resources allocated, the devil is in the details, and you will need to cure some childhood illnesses of the newly implemented solution before things mature. Hypercare is essential to not lose motivation and trust of your team. In the end, it will decide if your MES unfolds impact or not.
Keep a global roll out in mind early!
Implementing MES as a pilot is quite a bit of work to be done. Nevertheless, it is also a great chance to have first-hand experiences and to collect tons of lessons learned. Having this in mind, it makes sense to plan the transfer of this MES know-how to your global operations network.
The NEONEX approach to reach the best leverage effects is to set-up a clear pilot & follower plant strategy. This includes:
-
Definition of pilot plant concept for MES (one vs two)
-
Definition of know-how transfer concept (cross pilot plant vs pilot-to-follower plants)
-
Definition of roll out focus (maximized speed vs maximized functional completeness)
-
Definition of on-the-job involvement of follower plant experts (full time vs part-time)
Approaching a global roll out having a clear idea regarding these dimensions will help a lot to maximize efficiency and effectiveness gains by a solid know-how transfer. Typical gains and benefits of a well-run pilot implementation include:
- Standardized project methods & tools will support efficient & effective rollout globally
- Local process owner & key user setup work as blueprint for necessary global setup
- Defined standard processes work as MES baseline for other locations
- Using maximum checklists will reduce the risks for unforeseen situations
- Networking about pilot project experience will motivate other plants for rollout
Having a look at these dimensions, it is obvious that a well-planned pilot with the global perspective in mind will create a strong positive cost impact for the MES rollout to other locations. Furthermore, involving follower plants and global corporate functions will strongly support a global mindset beyond the mere topic of MES.
Establish a center of excellence if you want to get happy in the long run
Running an MES in a single plant is one thing. Running an MES in a globally distributed production network is a completely different one. First, you have to create a baseline of globally aligned operations processes to leverage the synergy potentials of standardization. Second, you have to agree on a set of globally valid KPIs that are calculated in the same way. This is to reach comparability of site performance, at least for the ones that will run comparable production technologies. And finally, you need a global concept to qualify your staff for MES on a local and global scale.
To provide governance and framework for all these aspects, NEONEX Best practice is to set up a global Center of Excellence (CoE) for your MES. In this CoE, competence, responsibility and standards can be generated and accumulated in a one-stop-shop to run your operations upon the technical backbone of an MES. If you want to be happy in the long run, this is the organizational structure to bring both IT experts and process owners to the table for defining standards, for educating global and local staff or to decide on upgrades to stay safe for future requirements or changes in technology to come.
Having those ten factors in mind when approaching an MES implementation and roll-out, the biggest failures giving people a hard life can be avoided. If a company does not have either enough or sufficiently experienced staff in place, it is highly recommended to select a partner for external support. If cost considerations dominate discussions, keep in mind that avoiding mistakes in an early phase will save you at least factor ten of expenses to get things back on track in a later phase. Therefore, choosing your partner wisely is a large lever for every company to smoothen its MES journey and to reach new levels of efficiency and process excellence.