Manufacturing Execution Systems: The believed dinosaur is more relevant than ever
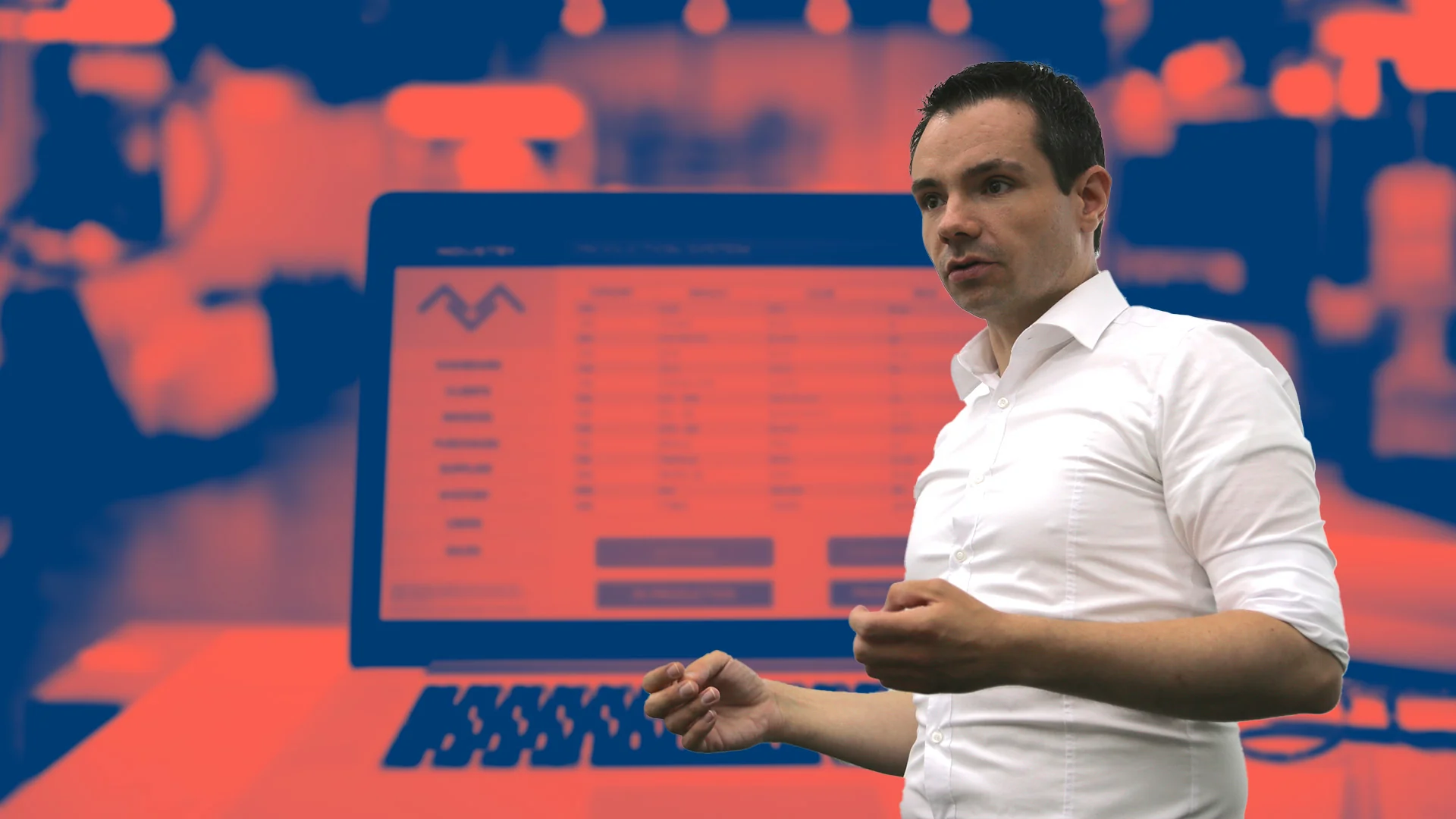
Is the believed dinosaur going to win Darwins race in Smart Manufacturing IT solutions?
Manufacturing Execution Systems (MES) are the believed dinosaurs of enterprise software systems for operations. Yet, Being around for more than 25 years and called to be dead or at least outdated for multiple times, they remain the technological backbone of operations for many manufacturers. Even more, today’s MES prove their robustness and ability to adapt by continuously integrating latest technology and increased user friendliness. This becomes obvious by looking at a few facts.
Better Functional Integration and UX-Design
Today’s leading MES solutions show an unseen level of functional integration between typical MES core functionalities and more advanced features & capabilities. Being historically equipped with core functionality around order management, order scheduling and operations data acquisition, big players have started to acquire companies & components to e.g. add enhanced tracking & tracing or advanced analytics functionality some years ago. Back in those days, MES looked more like a composition of LEGO bricks put together with some glue code and significant integration efforts during each implementation.
Today, vendors have managed to forge nicely integrated solutions that allow for an increasingly seamless integration between a wide and constantly growing range of functionality. Here’s how you can imagine that in detail:
- Vendors build on the solid foundation of MES being the central turntable for operations data on the lower end of the automation pyramid like no other system.
- Vendors can capitalize on already matured complex algorithms for scheduling & sequencing that reflect a major barrier for new market entrants
- Vendors are continuously integrating functionality to provide the best possible insights into collected shop floor data. This happens in three major time horizons:
a. Live Monitoring – to react with minimized latency on deviations and to minimize downtimes
b. Operational Analytics – to provide performance reporting and to drive CIP actions
c. Advanced Analytics – to correlate larger amounts of data e.g. to identify complex quality issues with a long-term perspective
Keeping that in mind, MES have the best position to remain the one-stop shop for every production supervisor to stay on track of its responsibilities.
Low Code Platform as Standard
The Low-Code-paradigm is becoming a standard functionality in a growing number of MES solutions. Originally being a class of its own, low-code-platforms provide unique abilities to easily develop individualized applications to process and represent data with a high level of user friendliness based on templates and a visual coding paradigm. Also coined as “the new excel in operations”, low-code-platforms are gaining high levels of attention and conquering their market share. From the perspective of MES, low-code platforms are a perfect add-on to traditional heavy-weight MES functionality like order scheduling & sequencing. Low-code-platforms are perfectly suited for providing a superior flexibility to a lot of MES functionality which are subject to customer-individual customization anyways. This accounts especially for:
- mall applications to quickly capture information from the shop floor by the human worker, e.g. in error reporting and deviation handling
- Set up of dashboards to display individually composed real-time information elements like order status, performance KPI or SPC Charts
- Generation of tailormade reports based upon customer process and customer roles e.g. for weekly or monthly standard meetings
- Modeling of workflows e.g. in problem solving or approval processes
- Modeling of business rules with logic relationships e.g. to generate constraints and boundaries for compliant processes
In these cases, low code platforms provide a huge benefit to the customer organization by empowering power user (often directly from operations) to quickly desire the needs for real-time transparency and guided workflows for fast and efficient decision making.
AI Co-Pilot as first true AI in Digital Manufacturing
Artificial Intelligence is one of the hottest topics discussed in Smart Manufacturing. And the discussion is often coined either by exaggerated expectations or by buzzword bingo. In such cases, it is often helpful to have a look at other domains and their way of adopting a new technology. If we look e.g. into the software development business, AI Co-Pilots are common features to support developers in writing code of higher quality in shorter time.
The adoption application of AI Co-Pilots is what we also see in modern MES. Focusing on supporting the human worker they provide assistance in the following dimensions:
- closing know-how gaps with superior problem classification and solution proposition abilities to speed up daily problem solving
- allowing for superior capabilities in doing data base requests to run ad-hoc performance analysis on operations real-time data
- providing natural language system interaction in both written and spoken form instead of manual search requests and logic specification of business rules
From an operations business value point of view this will result in higher productivity and shorter lead times as deviation handling and decision making will be both more efficient (reduced lag times) and more effective (based upon more precise analytics) as well.
The dinosaur is more alive than ever
Having the features mentioned above in mind, one must confess that the already written off dinosaur that is MES is more alive than ever. This is also proved by the number of 150+ vendors of MES on the European market. Therefore, it is highly recommended to have a close look at MES and their capabilities when running a digital transformation. To stay future proof, selecting the vendor with the right technologies and concepts on board is key.