Smart Factory - the value creation concept for the 21st century
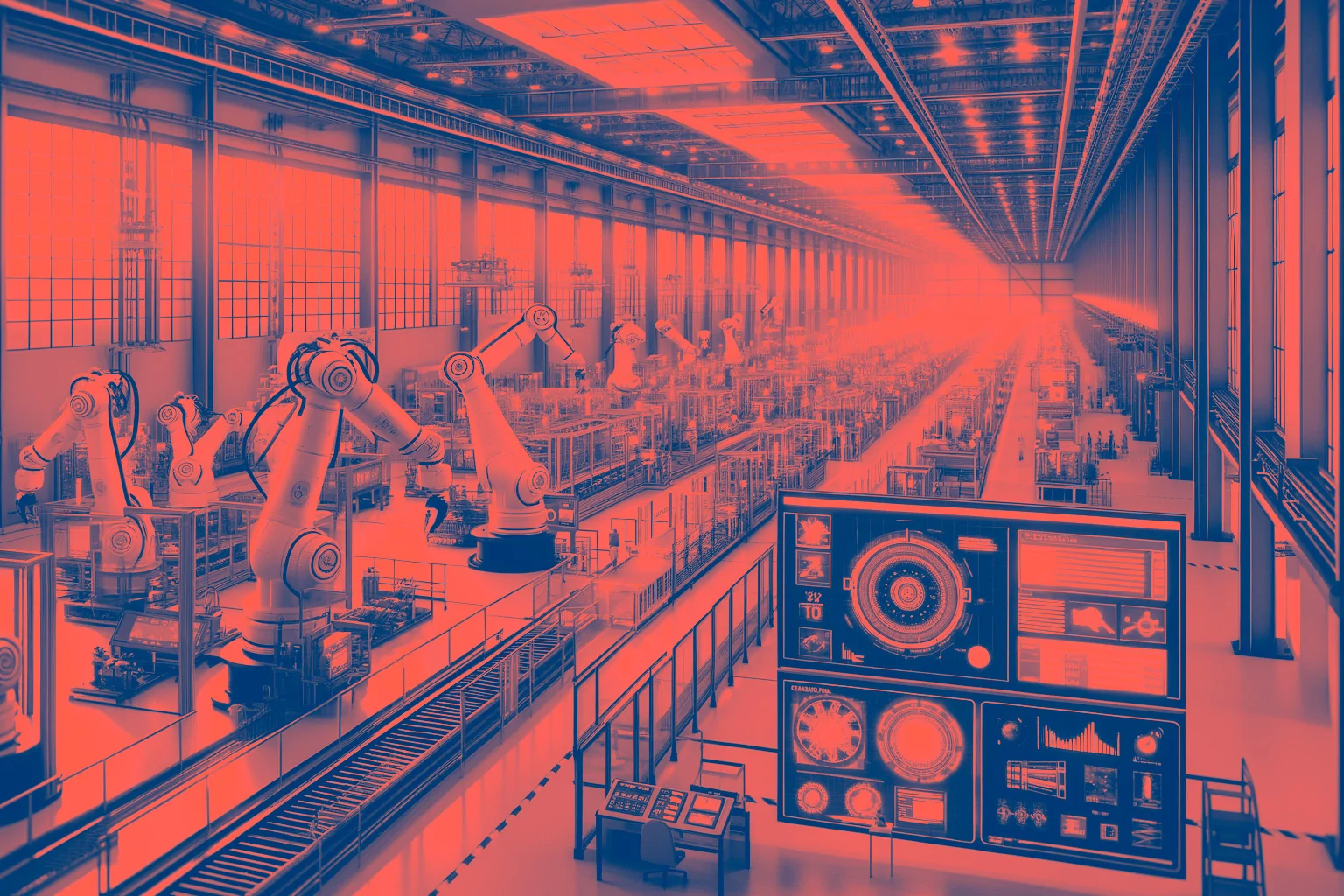
Your author & subject matter expert
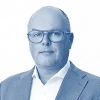
Thomas Rohrbach
Managing Director & Co-FounderManufacturing companies in Germany are faced with supply chain disruptions, fierce competition and customer demands for shorter delivery times and greater customization. In addition, falling market entry barriers are favoring new market participants. In this challenging situation, the smart factory, the "intelligent factory", is of particular importance.
In order to remain competitive, industrial companies should have started a digital transformation long ago. The strategies for this vary in terms of scope and impact on the business model: the biggest change would certainly come from platform business models or the disruption of the company's own business model. However, even without changing the business model, it is important to optimize operating processes through Industry 4.0 applications. Increased transparency and intelligent automation can lead to productivity gains. For German industrial companies, this optimization of operations is critical to success over the next five years. The target image here can be the smart factory, which represents an optimal combination of people, processes and (information) technologies.
Faster and more efficient: How the smart factory increases competitiveness
The most important feature of the smart factory lies in the horizontal and vertical data connections along the value stream (from incoming goods through production and assembly to outgoing goods) and the availability of data in real time. Against the backdrop of high volatility in corporate environments, this enables agility and flexibility: companies can adapt more strategically to their environment. Deviations can be communicated promptly and contextually to the respective managers. This relieves the management system of routines and significantly improves the quality and speed of decision-making.
In addition, this enables effective and efficient collaboration between people and machines or systems as well as between different IT systems used in a smart factory.
Another characteristic of the Smart Factory is its increased customer focus. Thanks to its increased efficiency, the smart factory enables lower prices, shorter delivery times, highly individualized products, ecological sustainability and a continuous improvement process. Networking, data availability and real-time data analysis also enable a higher degree of automation: systems can react to deviations, coordinate processes independently and plan maintenance work in advance, for example. Real end-to-end planning, mapping and implementation of value creation processes is feasible - and is becoming the standard in the industrial environment.
Ultimately, the smart factory is a learning ecosystem: a growing wealth of data can be used to recognize patterns and gain valuable insights (automatically). The aim is to increase efficiency. Not all of these features and their results can be achieved at the same time; instead, companies can set priorities based on their individual requirements and corporate strategies. The results of a smart factory have long been measurable: depending on the corporate strategy, the degree of utilization of operating resources, planning accuracy, the quality and speed of decision-making and delivery performance can be increased, while energy and material use, personnel costs, inventories, quality and maintenance costs are reduced.
A smart factory needs a solid foundation
In order for the smart factory to realize its potential, it needs a solid foundation consisting of several elements: lean, stable processes based on lean management principles and methods are required. Another important foundation is leadership and management excellence, which enables both the transformation and the actual efficiency of a smart factory. Of course, the maturity levels of lean enterprise and leadership do not have to be perfect at the beginning - but a good basis is helpful.
IT systems such as ERP (Enterprise Resource Planning), MES (Manufacturing Execution System), PLM (Product Lifecycle Management) and APS (Advanced Planning Systems), which use data and infrastructure to enable the mapping and handling of complex business, production, development and planning processes, also form the foundation of a smart factory (more on this in this special feature by Nathalie Kletti from MPDV). These systems enable technology applications such as analytics use cases (from business intelligence to artificial intelligence), augmented and virtual reality, mobile apps, additive manufacturing as well as automation and robotics applications (discussed in more detail in the article by Jörg Faber from MiR).
In order to realize a smart factory, companies should first develop a vision of their own smart factory 2030 with all its requirements. This target image can then be translated into a transformation roadmap, as the article by Bernd Hausler from ifm electronic impressively demonstrates. Such a far-reaching change is not trivial due to the large number of solutions and solution providers. In addition, there are organizational obstacles caused by the large number of stakeholders. As a result, it is not easy to master such a transformation - even though the changes in positioning and working methods are still relatively minor. However, if it succeeds, companies can significantly increase their customer benefits - and reduce costs at the same time.
So what are you waiting for?