Definition Value Stream Analysis
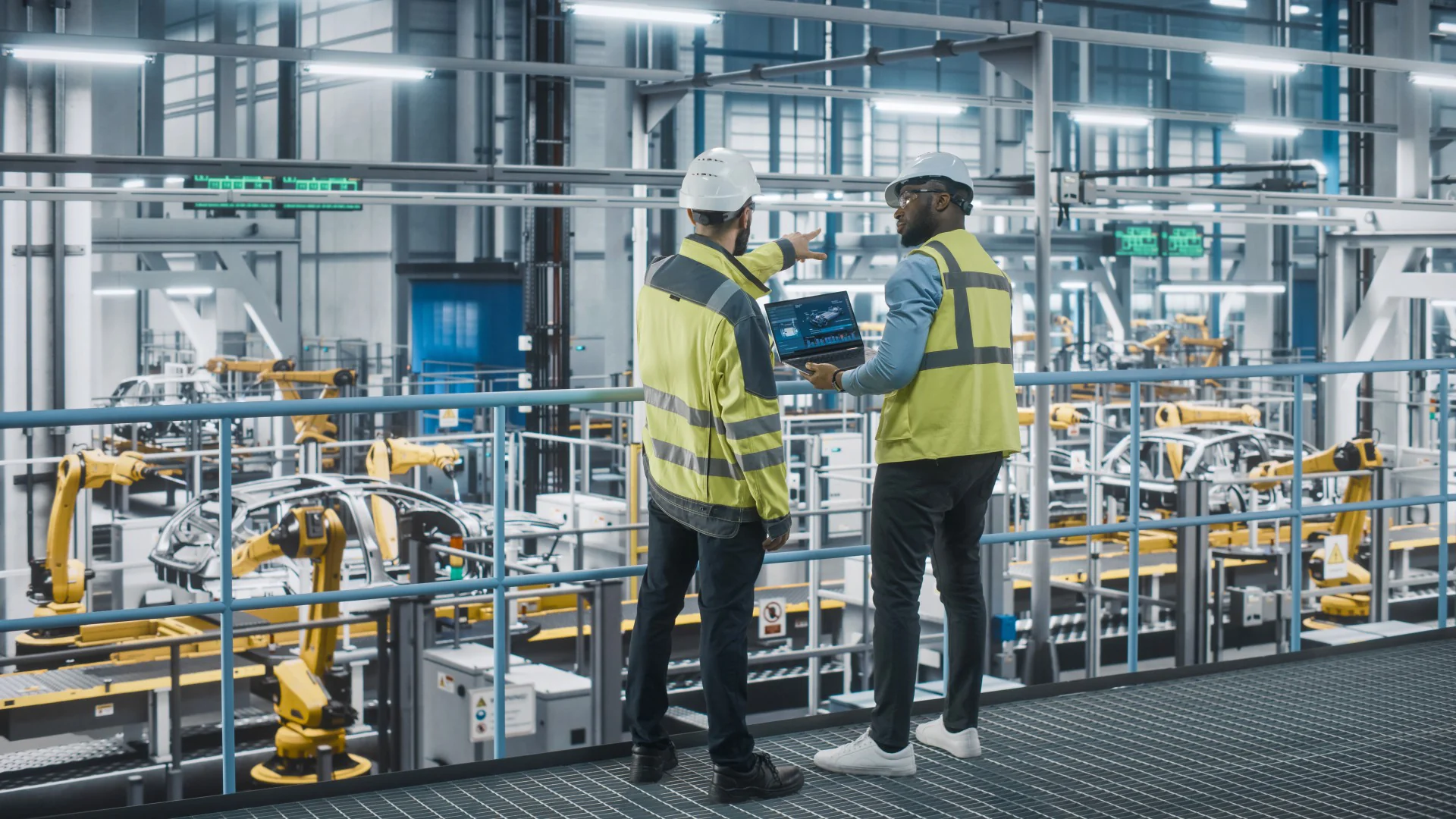
Your author & subject matter expert
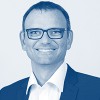
Dr. Jochen Schlick
Senior Partner & Co-FounderValue stream mapping is a method for depicting, analyzing and improving all material and information flows between customers, companies and suppliers as well as within the company that are necessary for the provision of a service (product or service) (see also: What is a value stream?). Value stream mapping, which has its origins in the lean methodology, is a flowchart method with standardized value stream symbols.
Value stream mapping is the first step in value stream management.
Aim of the value stream analysis
The aim of value stream mapping is to identify and eliminate waste or losses (muda) by mapping and analyzing the company's value streams. In the next step of value stream management, value stream design, an improved value stream is then designed in which non-value-adding activities and unnecessary idle times are eliminated.
Implementation of the value stream analysis
When carrying out a classic value stream analysis as part of the LEAN methodology, the value streams are usually viewed backwards from the customer through production to the suppliers. To do this, the processes are always viewed, understood and evaluated on site (jap. Gemba). In addition, pen and paper are always used and all affected stakeholders are involved.
Various digital tools can now be used as part of value stream mapping to significantly expand the possibilities for implementation. It is also possible to carry out the value stream analysis digitally on the basis of master and transaction data from various company software systems.
With both approaches, however, the underlying database should be carefully checked and, if in doubt, collected again.
Procedure for value stream mapping
1. segmentation
In the first step of value stream mapping, the company is segmented into individual value streams on the basis of a product-process matrix. As value stream management is used to design flow production with short throughput times, segmentation is based on the processes and material flows in the company. This contrasts with the principle of assembly for workshop production. However, this principle is not used for value stream mapping, as workshop production is not aimed at short throughput times.
2. customer cycle
In the next step of the value stream analysis, the customer cycle of each value stream is determined. This customer cycle describes the average required production output (in minutes/unit) based on the production quantity required to cover customer demand and the time available. Consequently, any process that runs faster than the customer cycle can cover the existing customer demand.
3. value stream mapping
As already described, a standardized value stream symbolism is used for value stream mapping in order to achieve a uniform understanding among all stakeholders involved. These symbols are made up as follows:
Symbols for value stream mapping
Production processes
The production processes are shown as boxes in which the key production figures are noted. These include, for example: Process time, set-up time, Overall Equipment Effectiveness (OEE), number of employees, batch size/container size, stocks, number of product variants, working hours/shift models, etc....
Material flow
Material flows between the processes are drawn depending on the material supply methodology:
- Pull connections (links without sequence swapping) are shown using the FIFO symbol.
- Push connections, where the preceding process determines the material flow, are represented by an arrow.
Intermediate warehouses are marked with triangles, under which the corresponding key figures are noted. These include, in particular, the stock level and the storage range. Warehouses managed using the Kanban method are sketched as supermarket shelves.
Information flow
In the last step of the value stream analysis, the information flow is recorded. This outlines how the production processes and warehouses are controlled. The symbols are based on those of the program flow chart.
Derivation of potentials
By presenting the operation as a value stream, two central optimization potentials can be identified. The aim is to reduce the delivery time from the customer's point of view and to increase capacity utilization in operations through uniform cycle coordination.
Flow rate
The flow rate describes the proportion of pure processing time (value-adding time) in the total throughput time. Times in which a product is not processed are idle times that are either unavoidable or waste that must be minimized.
Takt reconciliation
The cycle times of the individual processes can be compared with the customer cycle using a so-called cycle coordination diagram. Processes whose cycle time is close to the customer cycle indicate bottlenecks, while processes whose cycle time is significantly lower than the customer cycle indicate overcapacity and therefore waste.