Saurer
Intelligent Production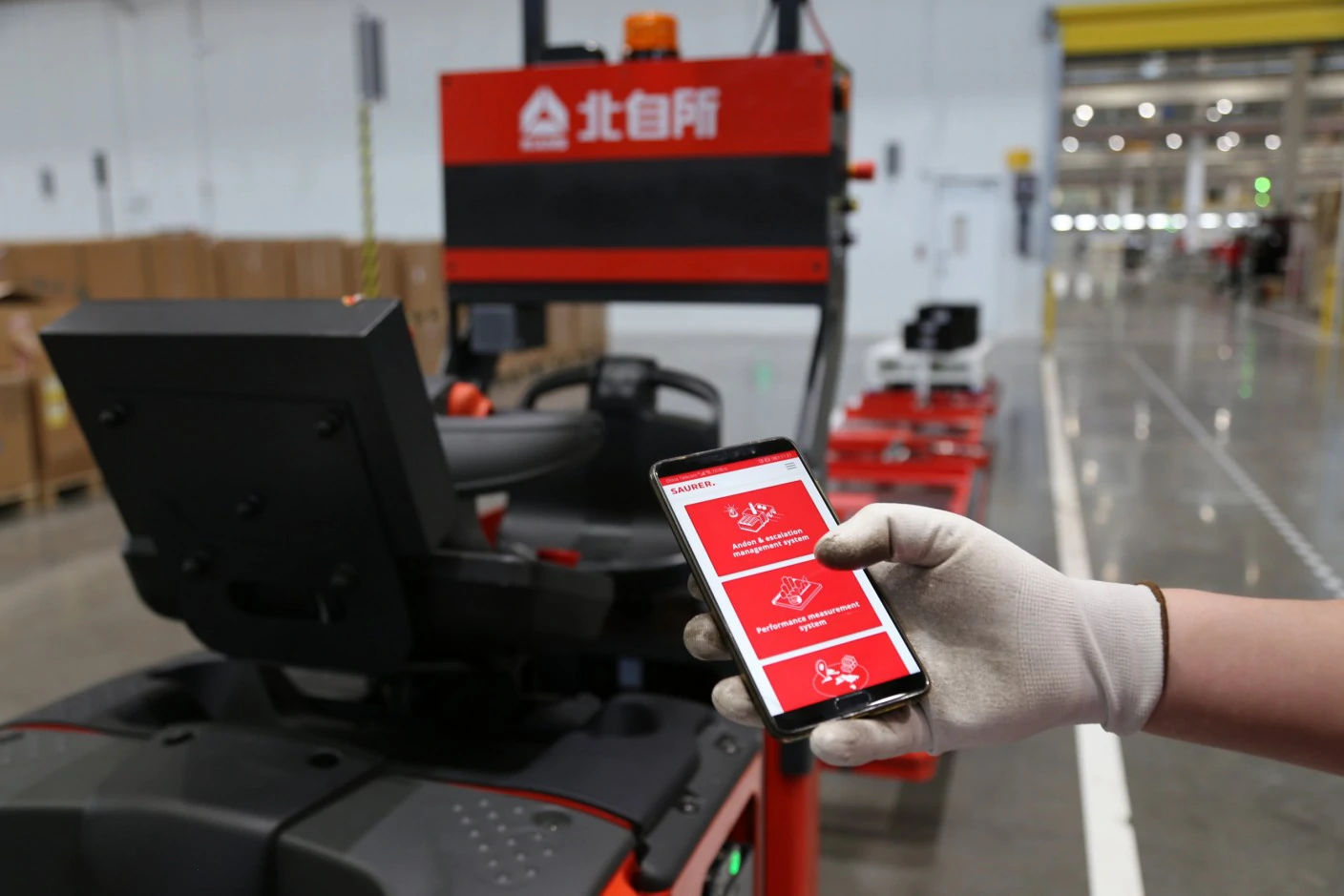
Smart Factory Greenfield Planning bei Saurer
👉 ☑️
Inhalte von YouTube werden aufgrund der von Ihnen gewählten Einstellungen zum Datenschutz nicht dargestellt. Um YouTube Videos zu aktivieren, gehen Sie bitte auf die "Datenschutzeinstellungen" und akzeptieren Sie alle Cookies.
Projektansatz
Das Projekt Saurer Intelligent Production konzentrierte sich auf eine Greenfield-Planungsaktivität zur Errichtung einer Smart Factory. Ziel war es, eine der modernsten und fortschrittlichsten Fabriken der Textilmaschinenindustrie nach den Grundsätzen von Process Excellence, Digitalisierung und Industrie 4.0 zu schaffen. Das Projekt begann mit der Entwicklung einer Smart Factory Vision, gefolgt von der Entwicklung detaillierter Konzepte und Modelle für spezielle Anwendungsfälle und der Definition von IT-Backbone-Systemen (Micro Service Private Cloud Platform und MES). Schließlich folgte die Auswahl von Lieferanten sowie die endgültige Implementierung und Einführung.
Umgesetzte Use Cases
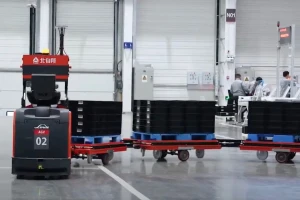
Smart Milkrun
- Automatisierung
- Intralogistik
Ausgangslage:
Der Materialtransport im Werk ist keine wertschöpfende Tätigkeit.
Digitale Lösung:
Automatisierung der Logistik mit einem Smart Milkrun
Autonom
Kein menschlicher Fahrer für den Materialtransport erforderlich.
Zuverlässig
Lieferung der richtigen Materialien an die richtigen Arbeitsplätze zur richtigen Zeit.
Ergebnis:
Freigegebene Kapazitäten
Mitarbeiter in der Logistik können jetzt stattdessen an wertschöpfenden Aufgaben arbeiten.
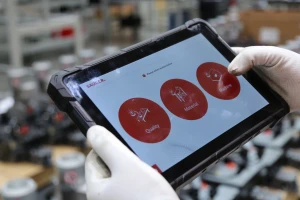
Andon & Escalation Management
- Andon
- Shopfloor
Ausgangslage:
Abweichungen werden nicht in einem strukturierten und geführten Prozess verwaltet, was die KPI-Verfolgung und kontinuierliche Verbesserung zu einer Herausforderung macht.
Digitale Lösung:
System für Ad-hoc-Abweichungsmeldung und -verwaltung
Mobile Reporting
Das Versenden von Anfragen zur sofortigen Unterstützung ist über mobile Geräte möglich. Die Moderation des gesamten Problemlösungsprozesses erfolgt innerhalb eines Systems.
Durchsuchbare Wissensdatenbank
Jede Abweichung wird standardisiert klassifiziert und gespeichert. KPI wie Mean Time to Repair (MTTR) können genau verfolgt werden. Eine durchsuchbare Wissensdatenbank über vergangene Vorfälle hilft dabei, zukünftige Abweichungen effizienter zu handhaben.
Ergebnisse:
Reduzierte Ausfallzeiten
Verringerte mittlere Reparaturzeit (MTTR)
Erhöhte Produktivität
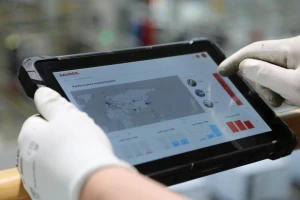
Performance Measurement System
- KPIs
- Automatisierung
Ausgangslage:
Die manuelle und papierbasierte Erfassung relevanter Daten für KPIs erfordert viel Zeit und Ressourcen. Es gibt keine standardisierten Formeln für die KPI-Berechnung zwischen Werken.
Digitale Lösung:
Performance Measurement System zur automatisierten und standardisierten Berechnung von Key Performance Indicators
Automatisiert
Berechnung globaler und lokaler KPIs basierend auf standardisierten Formeln
Weltweit zugänglich
Über jedes mobile Gerät innerhalb und außerhalb des Unternehmensnetzwerks
Benutzerfreundlich
Strukturierte und verständliche Visualisierung von KPIs
in Echtzeit
Entscheidungsfindung basierend auf aktuellen und richtigen Daten
Ergebnisse:
Bessere und zeitnahere Entscheidungen
Kürzere kontinuierliche Verbesserungszyklen
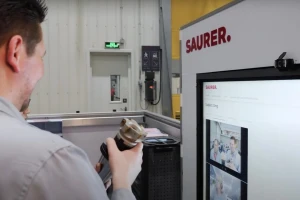
Remote Support System
- Digitale Kommunikation
- Support
Ausgangslage:
Das Abrufen von Expertenwissen an entfernten Standorten und Produktionsstätten während der Anlaufphase neuer Maschinen oder Produkte ist kostspielig und zeitaufwändig.
Digitale Lösung:
Remote Support System
Standortunabhängige Kommunikation
Kommunikation über Live-Chat anstelle von persönlichen Besprechungen oder asynchronem E-Mail-Versand
Weltweite Verfügbarkeit
Weltweiter Zugriff auf Maschinendaten, ohne tatsächlich vor Ort zu sein
Ergebnisse:
Expertenwissen ist an jedem Standort schneller und zu geringeren Kosten verfügbar
Effizientere und effektivere Problemlösung vor Ort
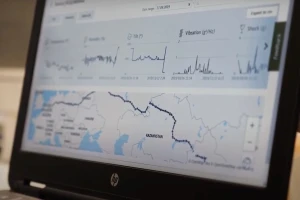
Supply Chain Transparency
- Supply Chain
Ausgangslage:
Die Ankunftszeiten von Material- und Komponentensendungen sind nicht vorhersehbar und daher ist die Produktionsplanung schwierig.
Digitale Lösung:
Sendungsverfolgung auf Basis aktueller Zustandsinformationen
Überwachung jeder Sendung
Ort, Status und voraussichtliche Ankunftszeit
Kombination von Sendungsinformationen mit Auftragsdaten aus dem ERP
Anzeige aller relevanten Informationen in einem einheitlichen Dashboard