What is a Smart Factory?
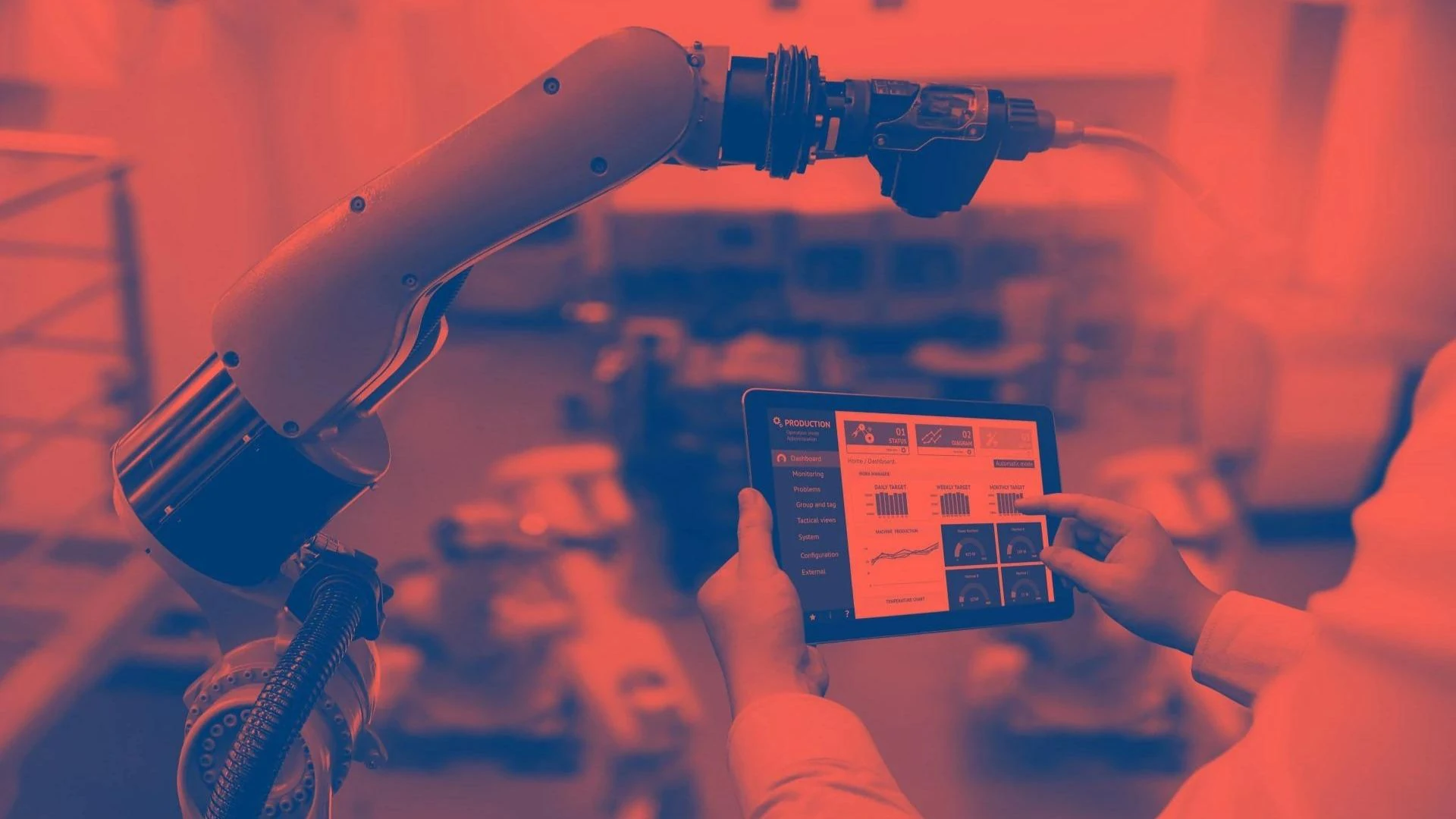
Your author & subject matter expert
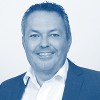
The term Smart Factory describes the concept of increasing the competitiveness of manufacturing companies by using and integrating digital technologies with IT, processes and people. The term is often used in the context of a digitalized store floor or an intelligent further development of the LEAN production system. In a smart factory, all systems, machines & processes collect data with the help of sensors, evaluate them and network them with each other in production.
By linking the physical world with the digital world in the form of data models, it becomes possible to plan, control and monitor not only the entire store floor and the entire production process, but also the entire networked supply chain, so that the increased complexity that companies have to handle, for example due to growing customer demands, becomes manageable.
The processed data can be used to increase the efficiency of direct and indirect value creation processes through automation, assistance systems or by people in real time. A Smart Factory makes production and supply chain flexible, adaptable and optimizable so that companies can sustainably secure their competitiveness through cost or differentiation features. But what exactly does the term smart factory mean? What are examples of smart factories? And which trends and technologies are used in the Smart Factory?
Explanation: Smart Factory
The Smart Factory describes a further development of the classic lean production including the first automation steps towards a completely transparent, networked and flexible production and supply chain. By using the data collected from operations, the smart factory can be constantly improved and adapted to new requirements in real time, or even improve and adapt itself using artificial intelligence.
The networking of value streams is possible through the continuous digitization of product master and process data. This digitalization is described in the so-called fourth industrial revolution (Industry 4.0).
Through digitization, physical and digital processes are connected with the help of information technology (IT) and operations technology (OT) and thus become easily multipliable and analyzable. This means that data from the production and supply chain of companies becomes available everywhere in real time, enables insights through human or artificial intelligence, and can thus be used for planning and optimizing production.
Thus, waste, e.g. in the form of downtime or scrap, can be avoided so that production becomes even more efficient and reaches a higher productivity level. This is particularly relevant against the background of growing customer demands, which are expressed, for example, in the form of requests for individualization and short delivery times.
In a Smart Factory, different degrees of automation are possible. For example, a smart factory is not automatically a dark factory in which no light is needed because no people work there and all tasks are performed by robots (such as intelligent, driverless transport systems). In the optimal Smart Factory, humans are supported by technology in their work in the best possible way. In addition, humans take over central maintenance and control tasks in the redesigned factory, and thus remain its turning and pivotal point in the future.
Due to the possible worldwide availability of the relevant data, the findings can be used not only in one factory, but also in the global production network. Thus, all factories of a company can benefit from the efficiency gains of other locations.
Characteristics of a Smart Factory
The Smart Factory is
- flexible and agile
- collaborative
- customer-oriented
- self-controlling
- efficient
- networked
- learning
Through the intelligent application of technologies, processes, IT and people, the Smart Factory is flexible and agile, i.e., it can react quickly to changes in, for example, customer needs or change proactively.
Since in the smart factory machines work with machines and machines work with people, the smart factory is collaborative. This is made clear, for example, by assistance systems in which people are supported by machines in a context-related manner, for example in augmented reality.
The Smart Factory is customer-oriented and could thus manufacture for batch size 1. This means that mass individualization is possible, individual products can be manufactured and offered at the price of a mass-produced product if this is required.
A smart factory is capable of decentralized control of itself. This means that individual systems in the factory can make their own decisions based on data analysis and modeling.
In the smart factory, production and logistics are extremely efficient due to the avoidance of all types of waste. For example, while production reduces waste in the form of overproduction, waiting or search times, logistics and the order fulfillment process is highly efficient through end-to-end data linkage, automation and real-time visibility.
The smart factory is networked: This means that processes are vertically and horizontally networked for optimal evaluation, control and improvement. Through the horizontal linkage between workpiece, process, & worker, the functional silos are dissolved. The value stream orientation is mapped not only in the material flow but also in the information flow. Vertical networking means that data is linked directly between the various corporate IT levels and no longer has to be passed through "layer by layer" in a time-consuming process.
Through the acquisition and (automated) evaluation of digital data, the smart factory is learning and improving itself. This means, for example, that reasons for inefficiencies or causes of errors are identified and avoided in the future. The Smart Factory is therefore becoming more and more efficient.
Smart Factory Technologies
Different technologies are used in a smart factory, depending on the degree of maturity and the goals sought. These technologies are primarily to be understood as "enablers " for achieving competitive advantages in a smart factory. However, a basic IT (Information Technology) and OT (Operational Technology) is always necessary in the Smart Factory.
A central component is sensors to collect data on the utilization, output and condition of machines and tools. Based on this data, information and insights can be gained.
The IIOT (Industrial Internet of Things) can be used to make the acquired data transparent to people and machines everywhere via the Internet, for example in an IIOT platform. This data can be used in real time or subsequently to make the production process more efficient.
With cloud computing, the data obtained can be stored, shared and analyzed at low cost. Cloud solutions can be more cost-effective and reliable than traditional on-premise solutions and are often easier to scale.
Big Data Analytics allows the evaluation of a large amount of acquired data to identify patterns in it that can be used for optimization of production. For example, statements about maintenance intervals (predictive maintenance) can be obtained.
With the help of KI (Artificial Intelligence) and Machine Learning, core processes of smart factories and supply chains can optimize themselves and make decisions that are normally made by humans.
VR (Virtual Reality) can be used to plan and test new factories, or to service existing machines remotely via the Internet. In this way, costs and planning risks can be lowered in planning and the planning time drastically reduced. In maintenance, a specialist for a specific machine or technology is no longer needed on site in a factory.
AR (augmented reality) visually connects the physical and digital worlds and can be used, for example, to graphically display information on installed parts in AR glasses. In this way, employees can be supported, for example, by displaying the correct tightening torques in AR while they are tightening a part.
Smart Factory Trends 2021
Rapid developments in IT are resulting in many new trends around the smart factory, so it should never be understood as an existing construct that cannot be changed. In addition, the arrival of many of the technologies mentioned above should be understood as a trend for 2021.
In addition to these technologies, there are several other smart factory trends:
To minimize machine downtime and failures, predictive maintenance is becoming more relevant for many companies. Insights from evaluating one machine can be used in the same or a different factory to reduce waste from machine breakdowns and thus increase manufacturing efficiency.
Humans remain a competitive factor in the smart factory because of their cognitive capabilities. To increase the efficiency of all tasks performed by people, the ergonomics of workplaces and processes is becoming increasingly important. Camera-based tools that evaluate people's movements can be used for optimization.
With the advent of the 5G mobile communications standard and the corresponding up- and download speed, new use cases for the IIOT are conceivable, since high data volumes can also be transferred on the move within a short time. It is thus conceivable to outsource even more complex computing services, which previously had to be performed on site due to the low latency required, while maintaining the same level of reliability.
With applications that cannot be mapped in the cloud due to particularly high data volumes or particularly short required latency times, such as camera-based evaluations, edge computing remains a relevant trend. Edge computing describes the processing of data as directly as possible at its source. For example, machines and tools can be equipped with computers that directly process the collected data. This processed data can then be uploaded to the cloud.
As a result of the technological possibilities described above, the trend towards mass customization will continue, as companies need to respond to corresponding customer needs in order to ensure their competitiveness.
RPA (Robotic Process Automation) describes 'software robots', i.e. computer programs that can be used to automate more complex business processes involving multiple data sources and other software programs. An example could be software that writes invoices based on data from multiple other applications without interfaces. Process mining, the automatic capture of processes to optimize them, must be considered in the context of RPA because it can be used to identify processes automated by RPA.
Smart Factory Transformation
Are you and your company currently in the transformation to a Smart Factory? Thomas Rohrbach, Managing Director of STAUFEN.DIGITAL NEONEX, has described three common challenges he has encountered again and again in numerous projects at NEONEX and his approaches to solving them in his "Connected" paper. Simply sign up for the free download here: