Smart Operations Cost Reduction
Initiatives for short-term cost reduction in manufacturing companies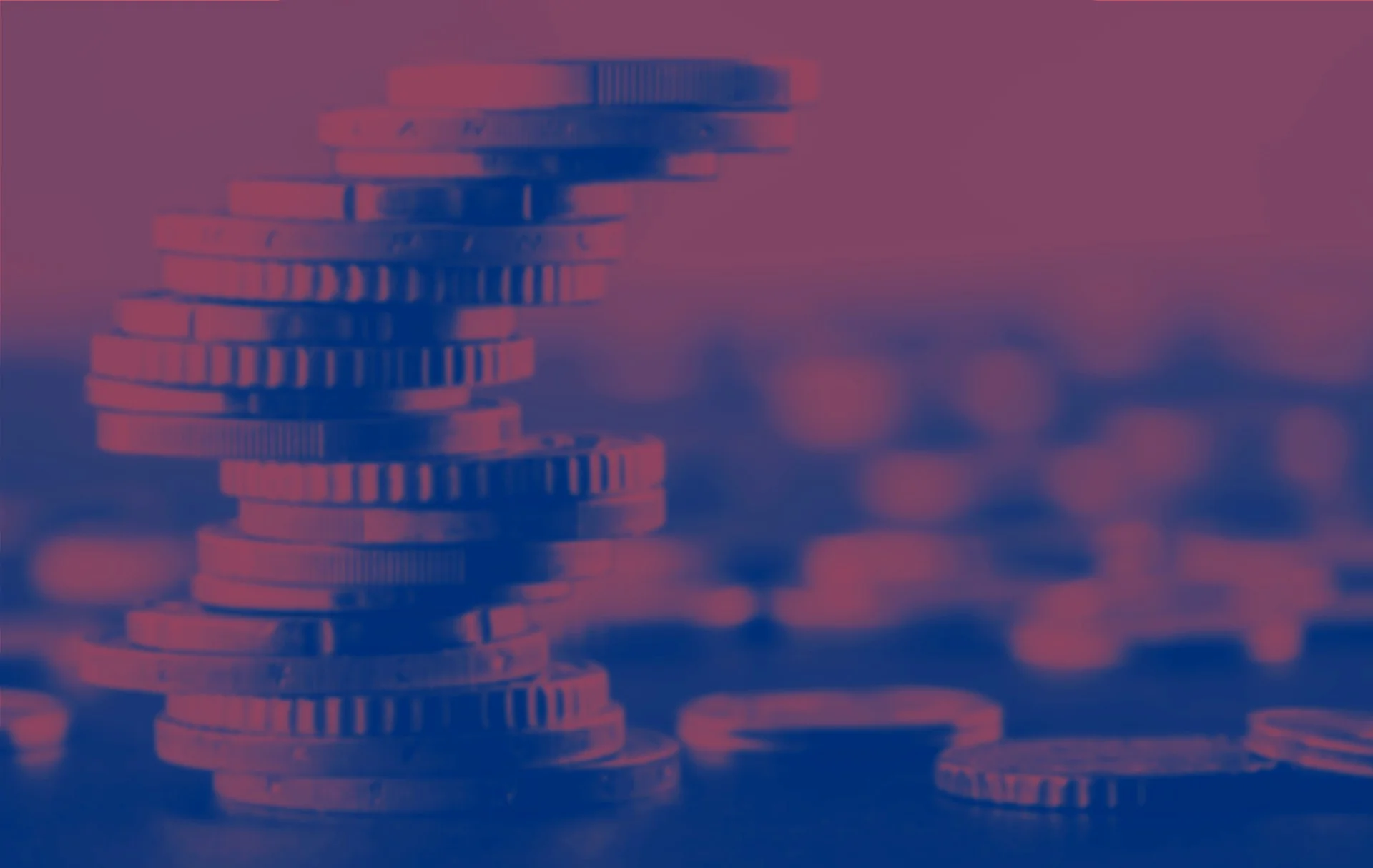
In addition to strategic issues such as sustainability efforts, labor shortages and supply chain problems, manufacturing companies, especially outside the growth sectors of high wage-markets, are suddenly facing increasing cost pressure due to declining order intake. This structural shift is new to many managers in the industry - after all, we can look back on almost 15 years of uninterrupted economic growth.
But how can you go about reducing your costs in the short to medium term? Fortunately, new times also bring new opportunities: through digitalization and data analytics, you now have the opportunity to identify and exploit cost reduction potential both more quickly and precisely. Based on these principles, we've put together a package of four consulting approaches that use our proven methods & tools to identify open potential in your operations and show a positive ROI within a few months, without any further investment:
Four consulting approaches for smart operations cost reduction.
DATA-BASED VALUE STREAM DOWNSIZING
With decreasing demand, cost reduction potential often arise in shift models and multi-machine operation. Based on your ERP-, MES-, forecast- and/or PDA- data, we determine how you can leverage cost potentials through planning, control and process efficiency improvements using an automatically generated holistic data model.
INVENTORY OPTIMIZATION
Inventories even slightly to big tie up liquidity and result in unnecessary storage costs. Especially when interest rates are rising and demand is falling, there is often great potential lying dormant here. Together with your scheduling department, we use your ERP data to analyze which inventories can be sensibly reduced. By building up stocks of selected items, we also increase your ability to deliver.
SCRAP COST REDUCTION
Through systematic manufacturing analytics applications, we analyze where the causes of the main quality problems in your production lie and how you can eliminate them to reduce material, machine and labor costs.
COST REDUCTION POTENTIAL ANALYSIS
In less than a week, we work with you and your process managers to analyze cost reduction potentials in your production, logistics and business processes. The focus is on the potentials that promises a break-even in less than one and a half years.
So regardless of whether you already have a clear picture of where you have cost potential or not: We offer you the opportunity to identify and/or monetize these potentials in the shortest possible time with data-based, focused methods. The methodical approaches are described in more detail via the download or down below.
DATA-BASED VALUE STREAM DOWNSIZING
When order intake falls, production capacities in shift models and multi-machine operation are often freed up. In order to reduce costs, it makes sense to eliminate these capacities. However, particularly in complex production environments with a large number of value streams and many shared resources, it is not trivial to identify and eliminate these overcapacities.
Therefore, we work with you and our team to build a data model based on ERP-, MES-, forecast- and/or PDA-data that enables the identification of precisely these potentials and supports you in achieving planning and control improvements as well as process efficiency increases. For this purpose, we analyze customer demand fluctuations, customer and production orders, lead times, batch sizes, pacemakers, backlogs, machine utilization, shift models and OEE with data from the last 6-24 months and a forecast for the next three years. Optionally, we also offer to simulate different demand scenarios and record corresponding adjustments per scenario to prepare you for all possibilities.
Investment: from € 25.000
Typical project duration: 2-4 months
Typical payback: 6-18 months
INVENTORY OPTIMIZATION
With increasingly broad product portfolios, planning the right amount of different raw materials and items is complex. However, precautionary overstocking now ties up expensive liquidity and results in storage costs of 9-18% of total inventory.
Together with you and your MRP department, we use our Inventory AnalytiX tool to analyze your ERP data to determine which inventories can be sensibly reduced based on consumption data, lot sizes and replenishment times. The proven benefit of this procedure lies in the knowledge of which inventories you can sensibly reduce in the short term on one hand, and the qualification of your disposition on the other. This way, no more excessive inventories are built up in the future.
Investment: from € 20.000
Typical project duration: 1-3 months
Typical payback: 2-12 months
Scrap cost reduction
Particularly when the causes of scrap are complex and multi-layered, classic methods from problem-solving technology often reach their limits, so that quality problems are not eliminated. Unnecessarily high costs for processes, material or rework are the result. Our approach supports you through systematic manufacturing analytics applications to identify and eliminate the reasons for quality problems in your production. To do this, we use data that you already have: ERP, MES or PDA systems, for example. This enables you to reduce material, machine and labor costs quickly and sustainably.
Investment: from € 15.000
Typical project duration: 1-3 months
Typical payback: 1-6 months
Cost reduction potential analysis
If you do not yet know where the cost reduction potentials in your production lie, how and in which order you can tackle them, our Cost reduction potential analysis helps you to systematically identify and document all potentials in order to eliminate them according to your roadmap. Together with you and your process owners, we analyze & identify all essential potentials in your production, logistics and business processes in less than a week. The focus is on the potentials that promise a break-even in less than one and a half years.
Investment: from 15.000 €
Typical project duration: 1-2 months
Typical payback: 4-18 months
YOUR CONTACT
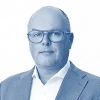
Thomas Rohrbach
Managing Director & Co-FounderInterested?
If you have any questions about this or would like to learn how we can help you get your costs under control in the short to medium term, please feel free to contact us!