ABUS
Smart OEE optimization on bottleneck machine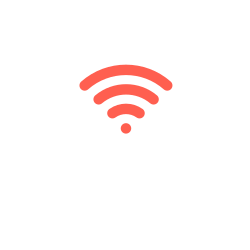
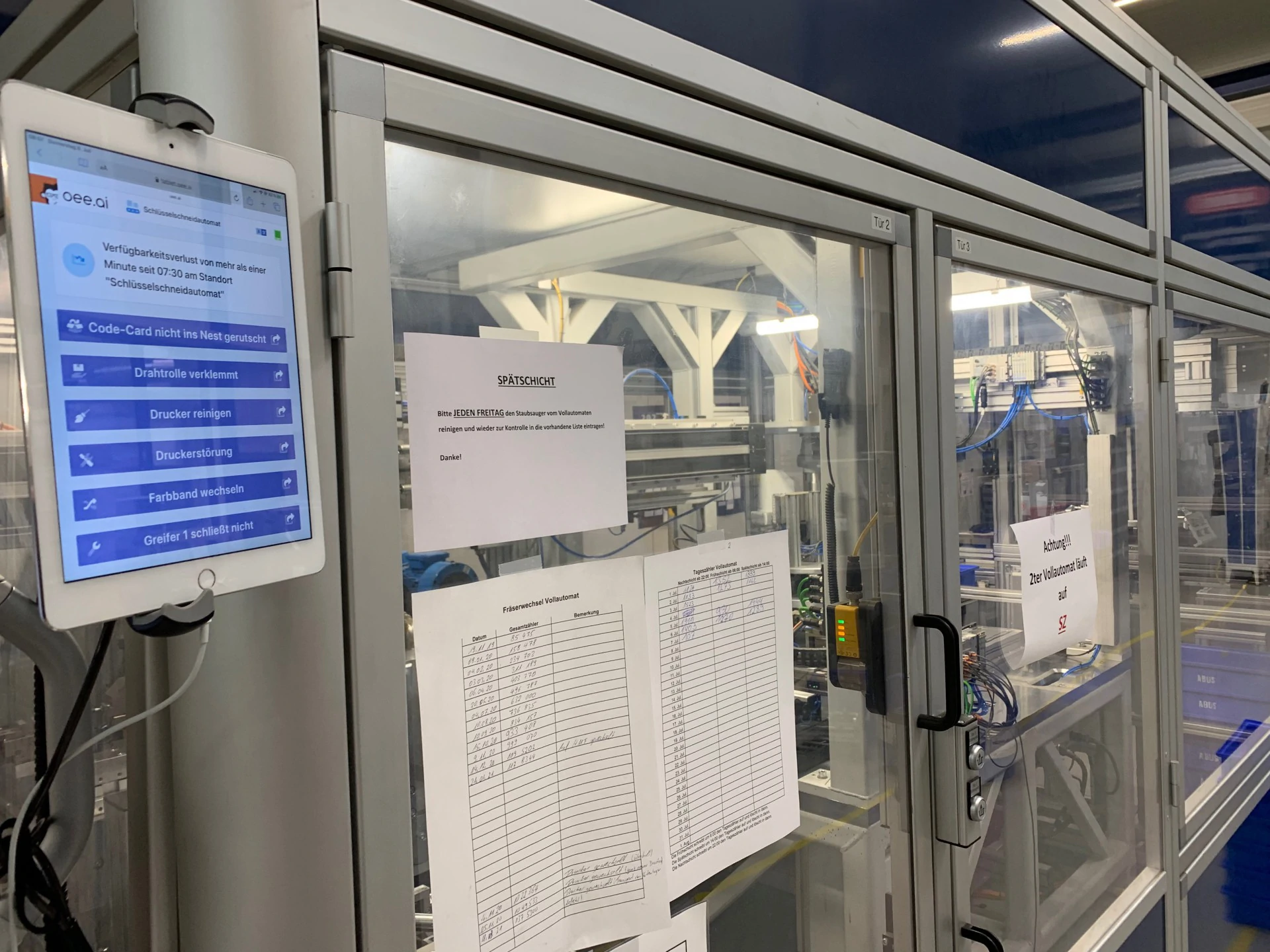
Project approach
The objective of the project with ABUS, the German manufacturer of safety technology, was to determine and eliminate the causes of downtimes on the bottleneck machine at the ABUS plant in Rehe. This was to increase OEE, create transparency in production and obtain important process data. Previous measures to increase OEE based on paper-based OEE management had not led to the desired results.
In order to quickly collect relevant data and derive the right measures, NEONEX consultants installed a non-invasive IIOT application from NEONEX partner oee.ai and supported the continuous improvement process (CIP) through regular OEE coaching.
For this purpose, about 10 reasons for loss on the bottleneck machine (planned/unplanned downtime) were identified in a joint kick-off workshop with Abus. Subsequently, a sensor for measuring the output quantity and a tablet for entering the reasons for downtime by the machine operators were installed on the bottleneck machine. On the software side, the IIOT platform was installed with the identified loss reasons and a custom Andon board with key KPIs. In the final step of the onboarding process, the awareness of the machine operators was raised through a joint workshop and the operation of the tablet was explained.
After onboarding, the initial measurement to collect reference values on downtimes and reasons for downtimes took place within two weeks. Subsequently, the collected data was jointly analyzed in the weekly OEE coaching, measures for optimizing the OEE were derived and the success of the previous measures was tracked. In addition, the NEONEX consultants were able to support the communication with the ABUS team.
The result for ABUS was impressive: losses were sustainably reduced towards zero and non-productive times were significantly reduced - a significant improvement in OEE in the double-digit percentage range.
The increased awareness of employees also led to shorter response times from operators and other departments and thus a reduction in Meantime to Repair (MTTR).
This also resulted in increased flexibility in shift scheduling for Abus. Communication between the direct and indirect areas was improved on the basis of the data obtained.
All in all, the results for Abus were impressive after only a very short time, despite the low effort involved.
Benefits for ABUS
Have we sparked your interest? In a preliminary meeting without any obligations for you, we would be happy to explain to you what Smart OEE Optimization can do for you.
Ihr Ansprechpartner
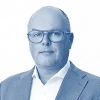