Advantages and disadvantages of a Smart Factory
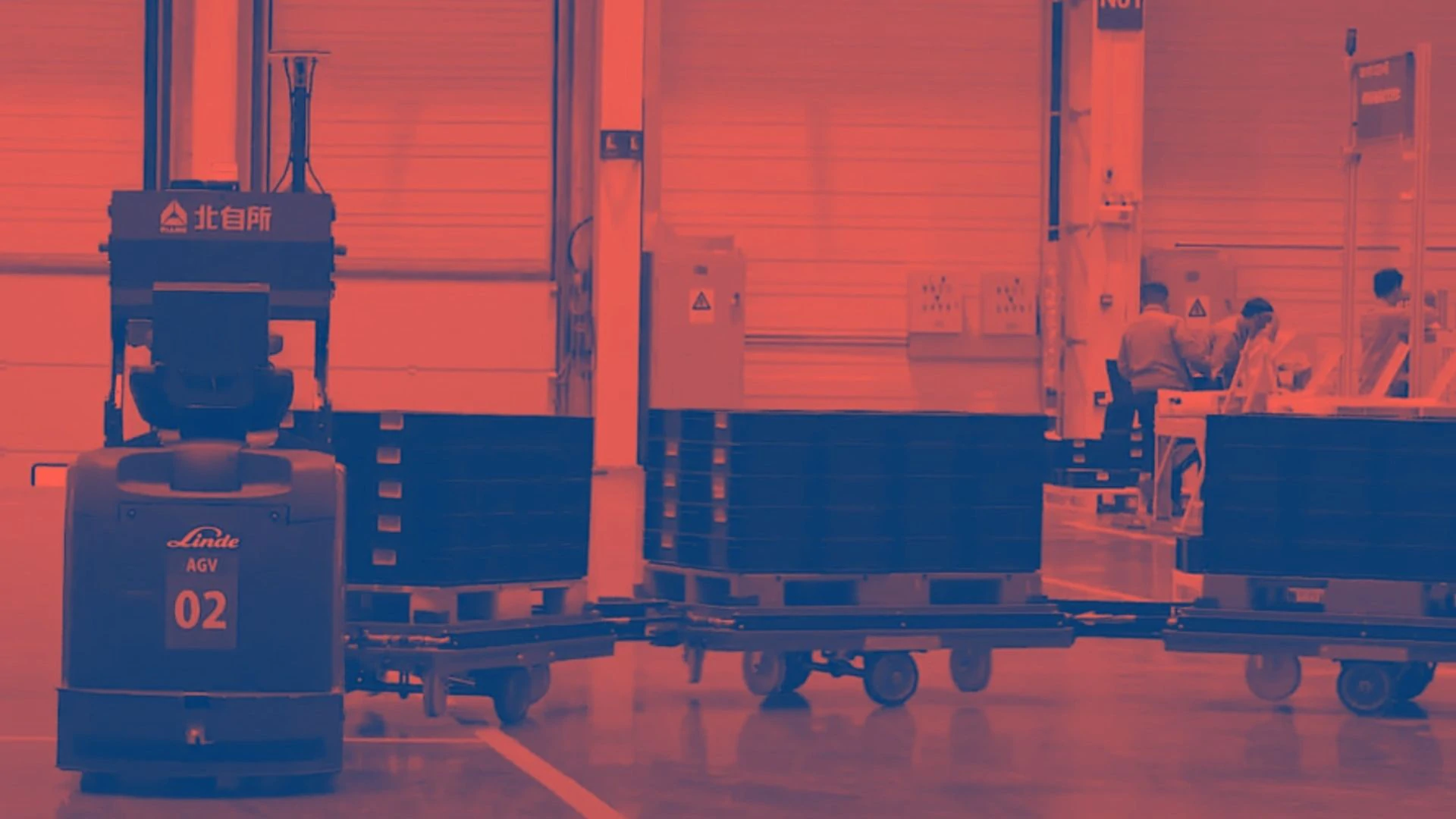
Your author & subject matter expert
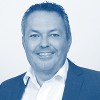
A Smart Factory has various advantages and disadvantages that arise from the combination of ever new technical possibilities of networking and data evaluation. We have summarized the main advantages and disadvantages of a smart factory for you.
The goal of a Smart Factory is to increase the competitiveness of manufacturing companies by using digital technologies and integrating them with people and lean processes.
The benefits of a Smart Factory are numerous and often concretely measurable. At the heart of many digitization initiatives is the increase in resource efficiency. Networking the entire value creation process and evaluating data creates transparency. This enables better plant utilization, planning accuracy, and the avoidance of waste and scrap. Automation or self-learning and predictive technology can increase productivity or reduce costs. Another advantage of a smart factory is its flexibility - this increases delivery performance and strengthens customer orientation, e.g. through the possibility of producing individual products to order at batch size 1 economically (with the same costs as in large-scale production).
The disadvantages of a Smart Factory are often cited as the complexity and cost intensity of the transformation process, as well as data protection concerns and the changed requirements profile for employees. Indeed, planning and implementing a holistic smart factory is a challenge. However, with the help of the right objectives and approach, which are clearly based on the individual advantages (depending on the respective business model) of a smart factory, these supposed disadvantages of a smart factory quickly fade into the background.
Overview of Smart Factory Advantages and Disadvantages
Advantages of a Smart Factory | Disadvantages of a Smart Factory |
---|---|
|
|
Advantages of a Smart Factory
Increase productivity, save costs: As our study "Digitalization 2020" shows, increasing efficiency remains the top motive for companies to opt for a Smart Factory. The advantage of a smart factory, increasing overall equipment effectiveness OEE, comes from several features of a smart factory:
Through the consistent, end-to-end use of digital planning & control systems in the Smart Factory, the entire operations areas are networked with each other - from planning to production, from incoming goods to outgoing goods. The resulting end-to-end transparency in the value-adding process is a major advantage of a smart factory: it can reduce lead times, reveal disruptions in the operating process, increase plannability and thus ensure increased productivity and lower costs.
The automation of production processes as well as self-learning, collaborative and predictive systems represent further advantages of a smart factory: Where route trains move autonomously through the production hall or materials are sorted by robots, employees in smart factories can concentrate on more complex tasks and (undetected) human errors can be largely eliminated or reduced. And where a machine already signals that the wear of a wear part will soon lead to failure, or an error in the production step will lead to scrap, unplanned downtime and follow-up costs can be avoided and delivery performance can be further increased.
Data-Analytics-Evaluations and technologies such as virtual reality, however, do not only become an advantage of a smart factory during ongoing operations. Lean, waste-free processes are a key success factor for efficient production. With the help of data analytics / process mining applications, bottlenecks and potential in the value stream design can be identified and, for example, the entire factory layout can be optimized. Virtual reality applications enable realistic planning of workstations with minimal effort. The Factory planning becomes step-by-step digital. The digital twin of the value stream, the factory is emerging.
But not only the increased efficiency can be considered an advantage of a smart factory: Increased transparency about production processes makes the smart factory flexible and agile: changes can be planned and implemented more easily, spontaneous customer orders can be realized. Above all, the production system based on information and communication technologies enables customized mass production (mass customization) and thus creates new customer benefits.
Disadvantages of a Smart Factory
The disadvantages of a Smart Factory usually do not arise during ongoing operations, but can be seen as challenges in planning and building the smart factory.
In many cases, the realization of a smart factory is a significant investment: new technology must be acquired and installed, and parts of the staff of the manufacturing companies must schedule working time for the planning of the digitization initiatives, the adaptations / modernizations of the IT systems and landscape, and training for the use of the new applications. The more fundamental and holistic the planned changes in operations are, the longer and more cost-intensive the transformation process will be. But selective solutions are often discouraged - at least in the long term.
Another disadvantage of a smart factory is that human conflicts can arise during the change process. First, in many cases, there is the question of responsibility and decision-making authority for digital topics. In some companies, staff positions for digitization exist, but their position is often limited compared to long-established general manager or plant manager positions. In operations, responsibility for digital is usually attributed to the IT department. Problems with acceptance of solutions can become a disadvantage in a smart factory if decisions are not actively made and supported jointly as part of change management.
Finally, automation and lean processes can also mean that previously existing positions are no longer needed. This widely feared negative side effect can cloud attitudes toward digitalization projects in the company. However, only in some cases is large-scale headcount reduction an explicit goal of digitalization projects. After all, the idea of the smart factory is not to replace people as far as possible with technologies. On the contrary, technologies should merely support the work of Smart Factory employees and make the value creation process more efficient. What is certain is that with new technical applications come changed roles and requirements for the qualifications of employees. New jobs may even need to be created to operate and maintain innovative systems and applications.
Perhaps the biggest drawback of a smart factory is the perceived complexity of decisions in the transformation process. Defining the target picture and selecting concrete digitization activities is a major challenge. First of all, in many places there is a lack of an overview of the technical possibilities and solutions on the market. Many managers fear that they will not be able to foresee the effectiveness of individual solutions and the interaction of all solutions. In addition, there may be disagreement about the concrete approach and sequence of implementation. In the end, the fear remains that a lack of know-how and experience will cause digitization activities to fail.
In data protection-conscious countries like Germany, data protection and data security are often explicitly mentioned as disadvantages of a smart factory, in addition to the above-mentioned challenges. Any networking of people and production and logistics systems can lead to personal data being collected, processed and possibly also transmitted with other data. Effective data protection in conformity with the GDPR must therefore already be implemented at the technology level. The processing of large volumes of data in the smart factory also always involves a security risk, as cybercrime and hacker attacks against companies are steadily increasing.
Overcoming disadvantages of a Smart Factory
You will notice: Real disadvantages of a smart factory can hardly be found for companies during ongoing operation - if the smart factory is planned with appropriate advantages. The critical success factor therefore lies in setting the right course during the setup phase. The motto: Take the maximum number of advantages of a smart factory, cleverly avoid or minimize the disadvantages of a smart factory.
For this to succeed, companies first need a coordinated objective for their smart factories that is closely interwoven with their business model. The development of a joint Vision, strategy and roadmap with those responsible from all operations areas not only ensures the holistic nature of the results, but also the necessary acceptance in the further procedure.
There is no 0815 standard solution for the smart factory; nor are all the technologies that are currently in vogue relevant for all manufacturing companies. Individual solutions must be found. It is important not to start with the technology: An ERP system solves problems only to a very limited extent if it maps inefficient processes. In addition, the employees who will later be responsible should be involved in the change process. Smart glasses for order processing do not add value if they are not used due to poor usability or employee involvement.
If companies approach digital transformation in a targeted, structured and holistic manner, they will be able to fully exploit the advantages of a smart factory and circumvent/reduce the disadvantages of a smart factory.
Does this sound interesting to you? We would be happy to support you along the way.