Smart OEE Optimization
Increase machine efficiency through non-invasive IIOT applicationBy increasing machine efficiency, manufacturing companies can reduce costs, exploit revenue potentials and thus sustainably improve their success. However, the data needed to take the right measures to improve the factors of plant efficiency (OEE) - availability, performance and quality - is often already missing.
This often leads to firefighting and short-term fixes rather than sustainable improvements, especially for bottleneck machines, leaving hidden potentials dormant in many companies. Our non-invasive IIOT application uncovers these hidden potentials quickly & data-based - with minimal investment for you.
Use data ... and knowledge of OEE optimization.
With Smart OEE Optimization we offer you the opportunity to increase your OEE by up to 20% within one year. To do this, we support you with our non-invasive approach with sensors and tablets that are placed on your machines and do not need to be integrated into your existing IT landscape. This way, you can collect relevant data on your OEE with minimal investment within a few days and derive improvement measures together with us in - first daily and later - weekly coaching appointments. You will also receive important data to increase transparency between the shopfloor and maintenance and thus also improve maintenance. After an initial proof of concept on your identified bottleneck machines, the solution can be scaled up and rolled out to further machines & plants so that your OEE can be further optimized.
Three steps to OEE optimization
Onboarding
In onboarding, we give you an introductory training, identify the congestion machine with you, and pick up your management team and staff so that nothing stands in the way of successful project execution.
Data-based OEE Coaching
In daily (first) and weekly (later) OEE coachings we help you to make sensible decisions based on the data obtained. The results are concrete measures for OEE optimization and loss reduction. In addition, our experts use an OEE Data Deep Dive to perform in-depth analyses of the losses in order to present you further results.
Rollout
After a successful proof of concept, we assess the rollout potential with you and prepare a roll-out to additional machines or plants.
Phases of Smart OEE Optimization.
- Week 1: Establishing real-time visibility. In the first week, we install IIOT sensors and tablets for loss detection on your machines, categorize OEE losses, and configure your dashboard for OEE optimization. Furthermore, we onboard your team.
- Week 2-5: Proof of Concept In the daily follow-up, we reflect on your output quantity, the losses of the day and discuss the loss reduction measures with you.
- Week 5-52: Sustainable OEE optimization. In weekly sparring appointments, our experts prepare an OEE deviation management and your maintenance requirements with you. In addition, we help you to prepare the roll-out.
Realized with our Tech-Partner OEE.ai.
Why NEONEX?
NEONEX is a management consultancy with technical and management expertise. We come from within industry. With our profound knowledge, we develop functional concepts to increase the competitiveness of our customers around the world and accompany them from the first step to the global roll-out.
Decide to sustainably optimize your plant efficiency and create relevant transparency in your manufacturing with Smart OEE Optimization.
Your contact
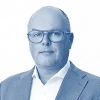
Thomas Rohrbach
Managing Director & Co-FounderResults
Increase your availability.
Increase your performance.
Increase your quality.
And increase your
OEE by up to 20%
*Based on data from previous customer projects.
Duration
One week to implementation, one year of weekly OEE coaching sessions.
Pricing
16.000,- € for a Proof-of-Concept on your bottleneck machine.