Pepperl+Fuchs
Smart Manufacturing Roadmap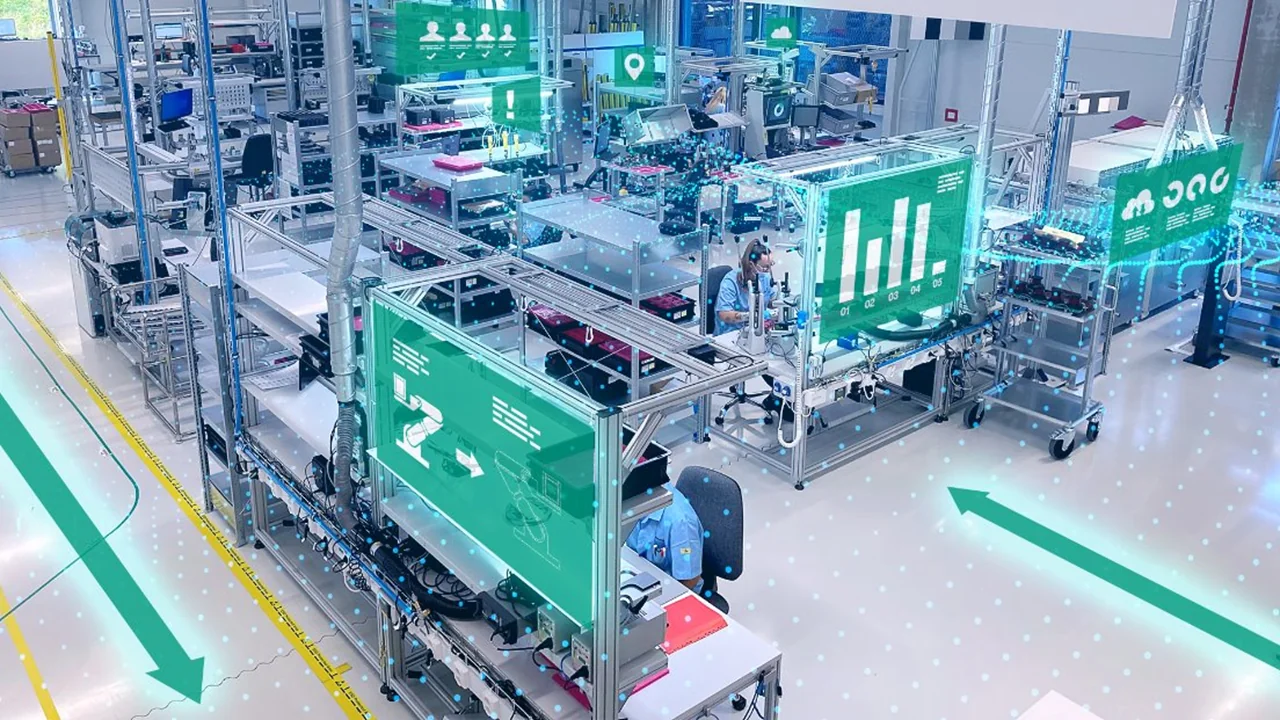
Start of the Smart Manufacturing Roadmap
The target of the project at Pepperl+Fuchs was to set up, design and successfully launch the global transformation initiative 'Smart Manufacturing Roadmap'.
The aim of the 'Smart Manufacturing Roadmap' is to significantly increase efficiency with digitalization as a lever for improvement potential beyond lean methods and to enable faster and fact-based decision-making, also as a basis for future partial automation. In addition, cross-functional collaboration and connectivity beyond the Shopfloor into indirect areas should be promoted and the organization should be prepared for greater digitalization maturity.
Project overview
As a first step, NEONEX consultants designed a qualification program for the core team at Pepperl+Fuchs, which primarily served to establish a common understanding and vocabulary in order to simplify discussions and decisions in the subsequent project work. Potential digital use cases were then identified at the production plants in the Czech Republic and Singapore using a standardized methodology. The required data and IT architecture and IT infrastructure were clarified and the use cases to be implemented were evaluated and planned using a global roadmap.
For this roadmap, system alternatives were evaluated for each use case, and use cases were clustered and sequenced. In addition, the allocation of use cases per plant, the pilot and rollout concept for the group (e.g. scale vs. scope) and the organizational and technical framework conditions for this were jointly developed.
Finally, NEONEX supported the Pepperl+Fuchs team in the requirements definition and structured selection of an MES solution provider, as this represents one of the central components of the future smart factory system architecture at Pepperl+Fuchs.
Benefits for Pepperl+Fuchs
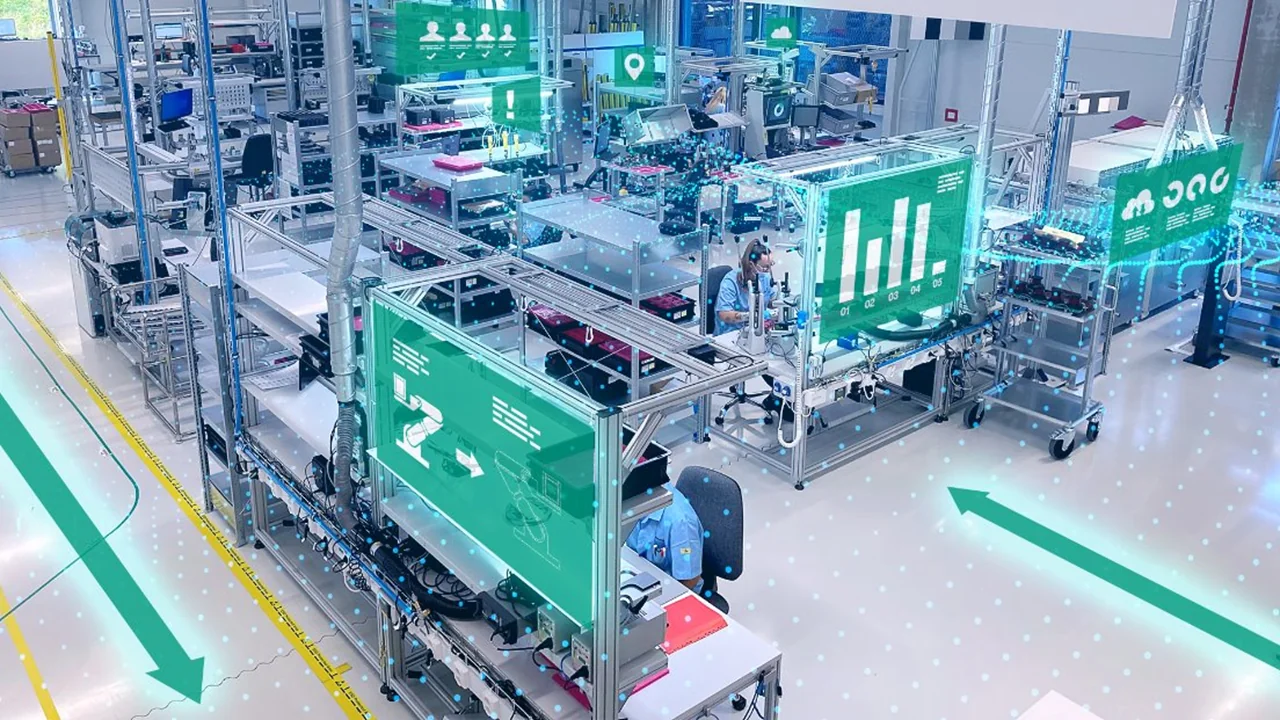
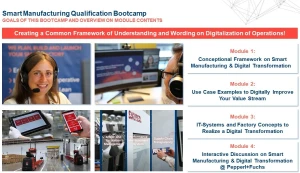
Smart Factory Qualification Bootcamp
- Qualification
- Inspiration
- Bootcamp
Target
The target of the Smart Factory Qualification Bootcamp was to create a common understanding and language on the topic of digitalization of operations in the entire core team of the project.
Methodology and tools
A four-day remote training course was held with more than 20 participants from four locations, during which the basics of a smart factory and the relationship between lean and digital were covered and initial results were developed, e.g. in the form of focal points for a later transformation.
Results
In addition to creating the same framework of understanding and the same vocabulary, the interactively developed results of the boot camp formed the basis for the efficient implementation of the subsequent analyses at two selected main Pepperl+Fuchs sites.
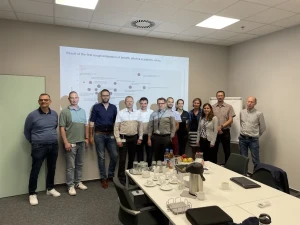
Smart Factory Potential Analysis
- Potential analysis
Target
The target of the Smart Factory potential analysis was the standardized identification and documentation of optimization potentials for later evaluation at two main production sites of the customer.
Methodology and tools
In the analysis for Pepperl+Fuchs, potentials for optimization in the plants in the Czech Republic and Singapore were identified along the value stream using Gemba walks and expert interviews. The identification and documentation was carried out in a standardized and fully digital workflow for maximum participation of the participants as well as for the efficient and transparent evaluation and selection of the top use cases.
Results
A total of 109 potentials were identified in the analysis at Pepperl+Fuchs, from which 42 use cases for planning & scheduling, real-time performance tracking, worker assistance & skill management, digital store floor management, smart maintenance, quality optimization, logistics connection, process automation & mining and asset management could be derived.
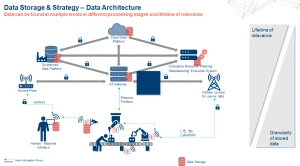
Data Management Assessment
- Data management
- Process data
- Transaction data
Target
The target of the data management assessment was to evaluate the current handling of operations data at Pepperl+Fuchs. In addition to examining the management of transaction and process data, the concepts and competencies for data processing were also analyzed.
It was also examined whether the role of the data owner was assigned locally or globally, how long which data was stored and when it was aggregated.
The readiness for cloud and advanced analytics solutions was also considered.
Methodology and tools
In order to carry out the assessment, an intensive week of analysis was spent discussing the issues raised, as well as looking at inputs and best practices from NEONEX to provide the Pepperl+Fuchs core team with a better understanding. For this reason, the week started with a sprint on examples of data-based decision making, followed by an inventory of existing data sources and already implemented analytics applications. This was followed by a look at data ownership and storage and the basis for data-based decision-making.
Results
The result of these workshops was a coordinated picture of existing and future data management for data-based decision-making.
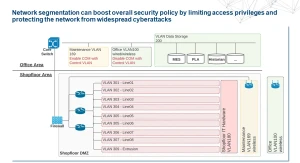
Connectivity and Resilience Check
- Shopfloor connectivity
- Network segmentation
Target
The target of the Connectivity and Resilience Check was to develop an organizational understanding of the implemented IT/OT connectivity and IT systems. This included determining the extent to which IT was controlled centrally or locally, the connectivity level of central shopfloor assets and how connectivity to ERP was structured. Finally, the shopfloor network architecture was also considered.
Methodology and tools
The joint workshop started with a short presentation on connectivity level best practices from the experience of NEONEX consultants, followed by lessons learned and pitfalls from NEONEX's project history. The site managers were then able to describe the connectivity levels of their own plants. In the next step, best practices for network segmentation were discussed and the existing network architecture of the Pepperl+Fuchs sites was recorded.
Results
During these workshops, it became clear that Pepperl+Fuchs had been strongly influenced by central IT in the past, so that there were few deviations in the foreign locations. Nevertheless, there were a number of special local solutions that had arisen from historical contexts.
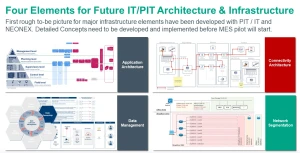
IT-System Landscape and -Architecture Review
- IT landscape
- IT systems
- IT architecture
Target
The target of the IT system landscape and architecture review was to record which make and buy IT systems Pepperl+Fuchs had in use or planned for future use. Furthermore, it was necessary to record which systems had been rolled out globally and which local systems were also in use. It was also to be recorded where Excel or purely paper-based documentation concepts were used.
Methodology and tools
In the first step of a four-stage assessment, the global IT system landscape with global and local IT systems and existing interfaces was recorded in order to understand which changes in this landscape were already planned for the future. In the second part of the assessment, the Czech Republic and Singapore sites were examined more closely with regard to order management, PDC/MDC, tracking/tracing, quality data, work instructions, warehouse management and dashboarding in order to record which functionalities were implemented in which system at this point. Finally, best practices with regard to the use of MES systems and IIoT platforms from other companies were discussed in order to subsequently identify basic requirements and framework conditions for a future architecture in an interactive discourse.
Results
The result of the assessment was the definition of a future vision that described the fundamental features of an adapted and future-proof IT architecture.
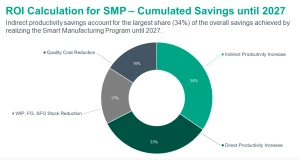
Ranking, ROI Calculation
- Ranking
- ROI
- ROI Calculation
Target
The target of the Ranking & ROI calculation was to define which use cases should be implemented globally based on the potential analyses and which should be implemented locally in individual plants. In addition, the identified use cases & systems were to be assessed and planned according to expected profitability.
Methodology and tools
A joint workshop was held to preselect the use cases, which were then analyzed in terms of ROI and break-even in the standardized NEONEX use case ROI calculation. On this basis, a strategic decision on the implementation and implementation sequence of the individual use cases was reached.
Results
The result of this step was an ROI calculation of the individual use cases and the overall program, which was used to approve the program and define an initial implementation roadmap.
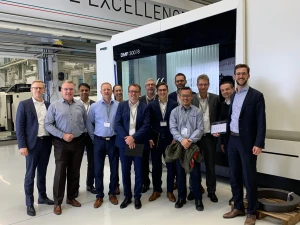
Smart Factory Tour
- Inspiration
- Smart Factory Tour
Target
The target of the Smart Factory Tour was the hands-on inspiration of the core team, especially with regard to the implementation of smart use cases and the IT architecture used by Industry 4.0 pioneers.
Methodology and tools
Individual reference visits were made to Bosch at the Feuerbach site and DMG MORI at the Pfronten site. The visit to DMG MORI impressively demonstrated how low-code platforms can be used for the rapid development of use cases. In contrast, the visit to Bosch showed how digital applications in their entirety lead to process and organizational optimization.
Results
The result of the Smart Factory Tour was the experience of smart use cases in daily industrial application as well as first-hand expert insight regarding the introduction and anchoring of systems and technologies in the organization.
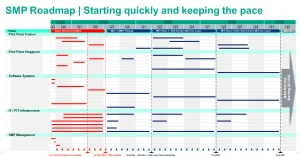
Roadmapping & program setup
- Roadmapping
- Setup
- IT architecture
Target
The target of the roadmapping and program setup was a final decision regarding the application of different IT systems as well as the implementation sequence and locations.
Methodology and tools
A decision was made between the architecture consisting of an MES system in combination with a low-code or IIoT platform against the background of the identified use cases. NEONEX consultants and the Pepperl+Fuch core team jointly decided that the identified use cases could be optimally implemented in an MES system and a low-code platform.
The use cases that are to be mapped in one of these systems in the future were then put into a logical sequence, which also included implementing selected use cases as a pilot with a smaller range of functions in the low-code platform in order to enable a later roll-out with the full range of functions in the MES. In addition, the use cases were assigned to the various plants according to a defined pilot-plan strategy in order to develop benefits against the background of the different product portfolios and to have the appropriate resources for implementation. These decisions were made on the basis of the ROI calculation, the plant conditions, the IT system allocation and identified dependencies between the individual use cases.
Results
On this basis, a program roadmap with timeline estimation and corresponding use case assignment was derived.
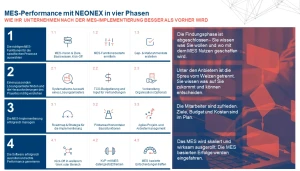
MES selection process
- MES assessment
- MES selection
Targets
As it became clear during the evaluation process that an MES system could already map a large number of the identified use cases at Pepperl+Fuchs as standard and thus avoid major expenses for the selection of individual solutions, the selection of an MES system was a key next step.
Methodology and tools
The structured and standardized NEONEX MES selection process was used to select the MES system in order to ensure a quick, transparent and coordinated decision and to take into account the scope of this decision.
For Pepperl+Fuchs, the degree of modularization of the system was particularly important, so that all solutions without a standardized API were filtered out right at the beginning, as they would not have allowed an interface to the low-code platform. A longlist was then drawn up on the basis of identified functional requirements and initial interviews were conducted with relevant providers. Non-functional requirements, including compliance, data security and documentation requirements, were also taken into account during the system selection process. Various selection considerations resulted in a shortlist of three possible suppliers. These three suppliers were invited to a supplier selection day, reference visits were made and a final deep dive into the systems was carried out. Finally, a commercial evaluation of the systems was carried out to enable a final decision to be made, taking into account the expected costs.
Results
Based on this method, an MES solution provider was selected quickly and efficiently.