Mabe
Digital Era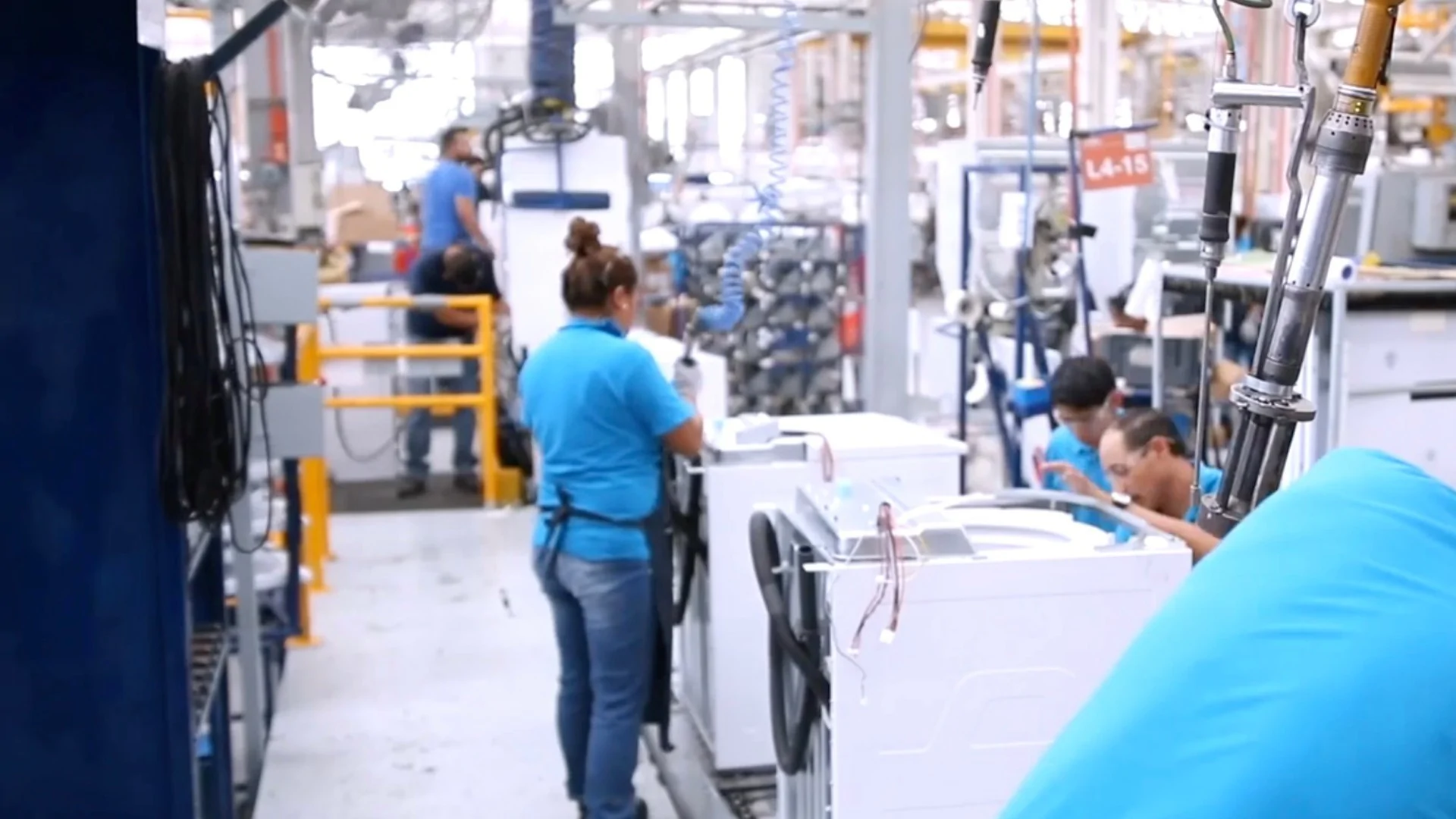
Off to a new Digital Era
Off to a new Digital Era
👉 ☑️
Inhalte von YouTube werden aufgrund der von Ihnen gewählten Einstellungen zum Datenschutz nicht dargestellt. Um YouTube Videos zu aktivieren, gehen Sie bitte auf die "Datenschutzeinstellungen" und akzeptieren Sie alle Cookies.
Initial situation
As part of Mabe’s extensive Digital Era initiative, NEONEX was asked to actively support the Digital Transformation of two lighthouse factories towards a higher flexibility, quality, customer orientation, adaptability efficiency, and real-time transparency.
Project overview
The As-Is Analysis in both plants in Mexico and a one-week Project Strategy Bootcamp in Germany led to the approach of a smart combination of proven principles, modern systems and use cases from the worlds of Lean and Digital, coupled with an adapted leadership style, to achieve the desired goals.
In total, 14 Smart Factory use cases were identified to be implemented. The introduction of a Manufacturing Execution System (MES) with a focus on connecting enterprise business processes with shopfloor execution including advanced planning, real-time operator support and real-time transparency is a major pillar of the transformation.
The proof-of-concept of "tangible" Manufacturing Analytics results established the base for a future in-house competence center for Manufacturing Analytics.
The evolution of corporate culture and leadership attitude, which is required to create maximum benefit, has been supported by leadership coaching.
Benefits for Mabe
Project Framework
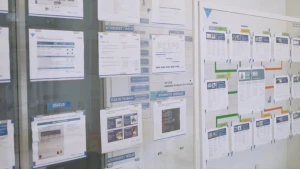
Digital Strategy for Operations
- Digital Strategy
Objective
The goal was to develop a digital strategy which sets the link between individual Smart Factory use cases within the operations and the top-level Corporate Strategy.
To do so, the future role of operations in the context of the future business model had to be worked out. The consideration of all relevant success and tech factors finally led to the detailed definition of a Cyber-Physical Production System combining the best of both worlds, Lean & Digital.
Methodology and Tools
Stakeholder interviews and a Digital-Potential Analysis were the base to develop:
- a Top Down Ideal Vision of Operations
- a Bottom-up use case Heatmap for prioritization
- a Bootcamp in Germany
- an IT System Backbone strategy
Results
At the end of the strategy phase, the entire Management Team had gained the same understanding of their own Digital Transformation and their objectives. A joint vision and strategy framework had been developed. A roadmap including required proves of concepts / pilot projects and roll-out plans had been successfully created.
This first step certainly was the key success factor of the whole Digital Transformation initiative, because the targets, aims, priorities, approaches and the project plan had been aligned between Top Management, Plant Managers and relevant Line Managers.
MES-Assessment and Implementation
- MES
- Supplier Selection
Objective
The aim of the module was to elaborate a target state for a wide range of business processes and the desired system support in the future. This relates to the production process as well as the link to indirect areas and performance measurement which is a core functionality of a Manufacturing Execution System (MES). A target picture was developed jointly and the integration of several use cases into the MES was evaluated.
The target picture and use case requirements lead to an overall set of MES requirements as basis for a structured supplier evaluation process and initial implementation planning.
Methodology and Tools
Joint workshops for future IT infrastructure and systems with Mabe’s process experts from different operational areas plus the corporate IT team were carried out.
- A MES Assessment was carried out to derive needs for future processes and use cases.
- Overall MES requirements were defined as basis for the MES supplier evaluation, MES implementation, and future development of Mabe based in the selected MES.
- A structured supplier evaluation process was carried out.
Results
In the first step, the need for an MES was assessed and a common understanding was developed among those involved (MES assessment). A structured evaluation process followed in order to define the required functions (MES Requirements definition) and to select the most suitable provider (MES Evaluation) based on functional & technical factors, commercial aspects, and soft factors. Finally, an implementation plan that fits to the overall initiative was derived.
Agile Project Management
- Agile Project Management
Objective
In a large and extensive project across multiple sites and project teams it is crucial to keep track on activities, dependencies and targets. An agile implementation framework was required to break down overall complexity into manageable pieces while being able to react flexibly during such a long transformation initiative.
Methodology and Tools
The underlying concept of keeping focus and short implementation times per Use Case was realized by working only on a few Use Cases at the same time. Each Use Case's level of detail is then increased iteratively to match users’ actual needs in the best possible way. Specific teams were defined for every Use Case with distinctive roles from Use Case leader and process owner to specialists and IT/OT support. These teams were working in a structured, yet responsive way on the implementation following
- An overall project roadmap with all Use Cases, MES implementation, Lean and Leadership initiatives
- An agile transformation framework for the pilot plants
- The NEONEX Use Case development and implementation approach with defined concept and development sprints
- Short-cyclic status reviews in weekly SCRUM meetings
Results
Resources were kept focused on few active Use Cases. Their sequence matched the overall transformation activities. Challenges and deviations could be identified quickly and tackled with countermeasures while the status was clear at any time. Working in this agile way ensured quick development and implementation times for each Use Case while keeping the overall project flexible enough to adjust to changing business needs and realize benefits in a user-centric way.
Implemented Use Cases
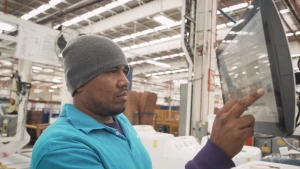
Quality Event Visualization
- Assembly
- Real time
- Visualisation
- Deviation Management
- Decision-making
Objective
The aim of the use case was to increase the assembly line performance through constant, systematic evaluation and visualization. Errors and deviations should be categorized in a structured way and thus be prioritized for fact-based deviation management.
Methodology and Tools
For this use case, the following NEONEX project sequence applied:
- Design Thinking sprints for definition of required functionalities and visualization
- Joint definition on data acquisition, data storage, data processing and visualization requirements
- Development of the whole user journey from automatic data acquisition, additional manual information input, evaluation and fact-based decision making
- Definition of a software development backlog for implementation by Mabe’s internal IT team
- Team qualification for continuously developing this use case for additional analysis and rollout scenarios
Results
The quick and easy analysis replaces manual data processing and evaluation and thus significantly reduces the time required for the activity. It represents a simple tool for daily use and immediate deviation detection. The evaluation is precise and error-free and enables the calculation and display of trends as well as extensive filter functions for the best possible prioritization.
Team leaders and Manager have now a real-time tool for their daily business – with significant positive impact on their First Time Yield (FTY).
As all information are collected in one data lake, Mabe’s process engineers are able to prioritize larger process and product improvement initiatives based on a top-down analysis with one tool and similar data without additional processing.
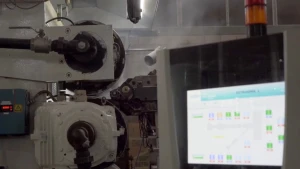
Energy Management
- Visualisation
- Sustainability
Objective
The goal of this use case was to reduce electrical energy consumption, especially in peak times. To do so, a transparency of electrical consumption and behavior over time needed to be created. Reporting and analysis functionalities had to be defined.
Methodology and Tools
The team followed our Neonex use case development process starting from a rough concept through detailed concept, supplier identification, supplier evaluation, implementation, and stabilization for rollout.
- The scope for the pilot area was evaluated and defined based on relative energy consumption, equipment complexity, and expected hardware and software cost
- Technical and functional requirements were defined for the pilot and future rollout scenarios
- A suitable supplier was selected in a structured supplier evaluation process
- The pilot was implemented and relevant reports were defined
- The team was qualified in the system and the methodology of optimizing energy consumption in a Kaizen workshop
Results
Remarkable energy saving potentials were identified and quantified and a real time transparency of base and peak consumption patterns was created (per shift / per day). Machine comparisons and benchmarking was introduced.
This acts as a fact-based support for decision making when it comes to investment and daily shift management.
Automation Roadmap & New Concepts
- Automation
- Value Stream Analysis
Objective
Labor cost for skilled workers is strongly rising in Mexico and the competition for talented staff is high. At the same time quality and performance expectations of the market are ever increasing. Smart and innovative automation concepts with a reasonable ROI (return on invest) had to be identified for supporting the production process and the existing automation roadmaps.
Methodology and Tools
Mabe’s process and automation experts were working jointly with our automation experts on
- Automation process analysis
- Automation concept development
- Cost and benefit evaluation
- Identification of potential product design changes
Results
The team analyzed the whole value stream together with top notch automation experts. Common understanding about automation opportunities and impact of product design changes became clear. Industry-specific process and automation challenges were addressed. Furthermore, the team was qualified in this structured analysis approach for future automation tasks.
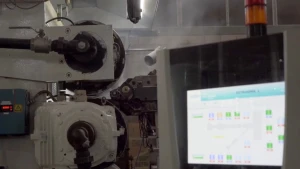
Manufacturing Analytics
- Data Analytics
- Performance
Objective
The goal was to describe the behavior model of complex machine processes and to identify internal and external influencing factors by using advanced Data Analytics.
The results should increase machine capacity and performance, reduce daily ramp-up losses and optimize yield.
Methodology and Tools
A variety of analytics approaches was applied to billions of data points from a complex and sensitive manufacturing asset. After identifying the best approach for data acquisition directly from the machine’s PLC in the first place, the team continued with
- Post-Processing and cleansing of the raw data
- Enriching the data with outside information like weather data
- Conducting various exploratory analyses
- Clustering and quantifying influencing factors on the machine behavior
- Developing advanced machine learning models
Results
An explorative analysis identified optimization priorities and concluded with advanced machine learning techniques. A cluster analysis revealed critical process parameters and improvement areas in the value stream process. A recommendation algorithm based on a machine learning model predicts optimal machine parameterization for increased process performance. Moreover, the identification of additional machine instrumentation requirements, data recording and data processing competencies were developed at Mabe and helped to improve machine performance.
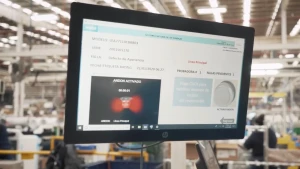
Andon & Escalation Management
- Andon
- Shopfloor
- Real-time
- Visualisation
- Decision-making
Objective
The aim of this use case was to increase the overall performance and efficiency of problem-solving activities on the shopfloor. Therefore, a quick response and feedback system that allowed integrated realtime support for Managers, Team leaders and Engineers should be developed.
Methodology and Tools
The team developed this us case to support Mabe’s organization in the best possible way according to the NEONEX use case implementation approach including
- Development of all information and escalation flows
- Automatic and manual data acquisition concept and case-specific workflows
- Tracking of all deviations on the shopfloor and definition of related KPIs for continuous improvement
- Definition of required hardware and infrastructure
- Alignment with the software integrator to realize this use case within the MES
Results
By capturing deviations on Manufacturing processes in detail and classifying the deviations in a standardized manner, transparent, structured, automatic workflows for guided deviation management were developed.
With the help of this use case, the following results were achieved:
- Reduction of Mean Time To Repair (MTTR) / Mean Time To Attend (MTTA)
- Reduced losses leading to higher OEE and output for machines and assembly operations.
- Overall performance increase
- Common data base for structured process improvements by industrialengineering
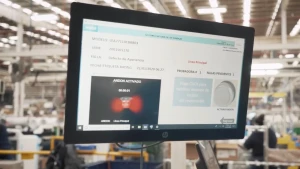
Asset Performance Management
- Automation
- Visualisation
- Decision-making
Objectives
The goal was to establish an increased asset availability in the areas of thermoforming, stamping and injection machinery without larger CAPEX investments by real-time transparency. To achieve the goal, manual data acquisition and processing should be replaced with an automated process. In addition, relevant indicators should be visualized in a user-oriented manner and be available to employees at all times.
Methodology and Tools
The team developed this use case according to the NEONEX use case implementation approach including
- Definition of relevant KPIs
- Definition of simple yet powerful user-group-oriented visualizations from operator level up to the plant director
- Automatic and manual data acquisition concept
- Tracking of all deviations on the shopfloor
- Definition of required hardware and infrastructure
- Alignment with the software integrator to realize this use case within the MES
Results
The established data base offers valid real time information throughout all organizational levels. Therefore, it acts as the plant’s leading management instrument (one single source of truth) in operations as well as in process engineering. User-friendly visualizations allow quick reaction in case of deviations on the shopfloor while historic evaluation allows for focused long-term improvements.
Advanced Production Planning & Scheduling
- Production Planning
- MES
Objective
The aim of this use case was to replace manual planning processes with system-based planning and scheduling support. Long, interconnected process chains in the plant require perfect synchronization to meet the customer demand efficiently. Manual planning efforts were to be reduced while the planning accuracy was to be increased to allow more efficient asset utilization.
Methodology and Tools
The team developed this use case according to the NEONEX use case implementation approach including
- Definition of relevant planning scenarios and functionalities
- Identification of relevant master data and planning premises
- Definition of deviation detection and use of alternative planning scenarios
- Alignment with the software integrator to realize this use case within the MES
Results
System-based planning increases the control over the plant and ensures that all manufacturing areas are operating in a synchronized way. A better match of available production capacities with market demand helps to operate the plants more efficiently and more market-oriented.
Smart Workstation
- Shopfloor
- Support
Objective
The target of this use case was to support operators during the manufacturing and assembly process in real-time. Digital production orders, digital work instructions and pick-by-light should reduce the risk of wrong assembly or wrong machine setup even with an ever increasing product portfolio and the related complexity in the plant.
Methodology and Tools
The team developed this use case according to the NEONEX use case implementation approach including
- Detailed concept with all workflows and process scenarios that had to be supported by the system
- Definition of relevant information, data, documents to enable real-time support on the shopfloor including a smart way to limit master data generation as much as possible
- Identification and evaluation of suitable hardware suppliers
- Alignment with the software integrator to realize this use case within the MES
Results
This use case supports operators during setup of machines as well as assembly staff in critical operations. Innovative workstations can increase the quality even further and help to deal with rising complexity. Moreover, they allow the operators a more flexible utilization as the system supports them when necessary.