The future of German manufacturers: Seven key maxims
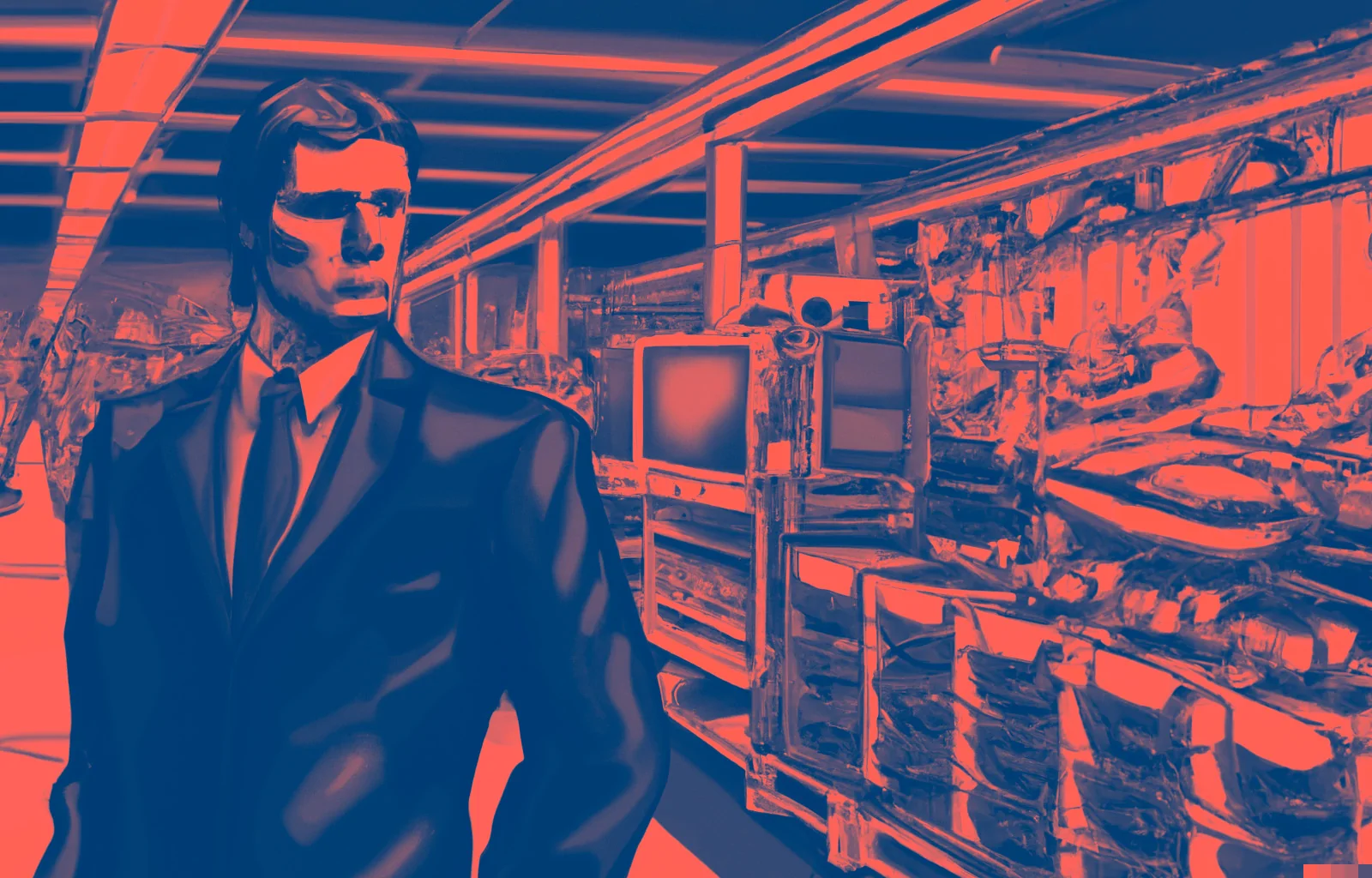
Your author & subject matter expert
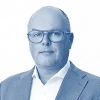
Thomas Rohrbach
Managing Director & Co-FounderEconomic factors such as rising energy costs, unstable supply chains and an outdated infrastructure are putting the future viability of German industry to the test. Social factors such as an aging workforce, the associated loss of experience and a general shortage of skilled workers are making it even more difficult to create sustainable industrial value. These are framework conditions that are putting the competitiveness of manufacturing companies to the test in a market characterized by changing customer behavior with growing demands for individualization, real-time information and sustainability in the face of rapidly growing foreign competition.
To meet these challenges, industrial companies must (finally) launch into their holistic transformation. This transformation begins by breaking down the corporate strategy with all competitive advantages for all corporate divisions. Since the competitive advantages of German industrial companies in the past arose primarily from production and logistics - i.e., from the ability to deliver the quantities required by the customer at the right time at the right price in top quality - these areas are particularly significant. Against this background, seven fields of action emerge:
1. Automation
Automation technology has made considerable progress in recent years and is now much more powerful and cost-effective than it was a decade ago. Consequently, companies can now efficiently automate significantly more processes in the direct and indirect areas. For example, physically impaired employees can be relieved by the use of intelligent, modular robots, unskilled employees can be supported by assistance systems, or personnel resources can be freed up entirely for value-adding activities. This reduces costs and counteracts the worsening shortage of skilled workers.
2. Digitalization and networking
Digitization and networking of all direct and indirect industrial value creation processes opens up the possibility for managers to achieve complete real-time transparency for the first time. This transparency enables ad-hoc intervention in the event of deviations and allows more informed decisions in the sense of a continuous improvement cycle. Decisions can now achieve measurable results more quickly, systemic and complex interrelationships are clarified and can be used in day-to-day business.
3. Systemic understanding
Many companies have already successfully implemented individual automation and digitization use cases as lighthouse solutions. However, the actual benefits are often unclear so far and synergies remain untapped as long as these implementations are not considered as part of an "end-to-end" value chain. To achieve the full efficiency and scalability of automation and digitization solutions, vertical functional, data and process silos must be broken down. Achieving this goal requires a holistic approach led by experienced process managers who can think outside the functional box and design a end-to-end process target picture.
4. Data analytics
Companies that want to successfully manage an increasingly complex production and supply chain need to focus on a new core competency: Data Analytics. Data-driven insights are essential to perform fast and correct analyses in the future, to provide impact correlations and to ensure decisions are made. Much of the data required for this is already available or can be easily collected. The range of analytical methods is enormous. Everyone is talking about artificial intelligence - but simpler analytics approaches are already sufficient to provide answers to very many questions. In a modern value creation system, data management and analytics are a fundamental prerequisite for sustainable competitiveness.
5. Knowledge and complexity management
Manufacturing companies are facing a threefold generational change that poses special challenges for them: On the one hand, there is a new generation of customers who demand faster delivery times and greater individualization. Second, there is a new generation of products with a higher degree of modularization that enables companies to meet these demands. Finally, there is a new generation of employees who need to benefit from the experience and knowledge of more experienced employees in order to master the complexity of the new product generation. Only companies that view knowledge and complexity management as a central element of their strategy and successfully implement it will be able to successfully master this change.
6. Sourcing strategies.
Given the breakdown of global supply chains, it is not only the unreliability of these systems that is becoming apparent, but also the rising transportation costs and emissions that have accompanied them. In addition, it also reveals the vulnerability to faulty planning due to long transportation times and the accompanying delays in meeting rapidly changing customer needs. To overcome these challenges, companies can localize their production and rethink which components can be reasonably manufactured locally. Given advances in automation and digitization, the lost cost advantages of the past have long been compensated for. Furthermore, local manufacturing offers the added benefit of automatically being more environmentally and economically sustainable, as any form of waste in the processes would be far too costly.
7. Agile fulfillment of customer needs.
Companies that use automation and digitization to create a value creation system that takes the above points into account are not only able to operate more efficiently, but can also respond to changes in customer needs at short notice, thereby increasing their agility. This leads to a positive impact on the revenue and cost side, as these companies can quickly adapt themselves, their structures and products to the changes.
To successfully launch this transformation, German business leaders must shed the technology and risk aversion they seem to have developed. The first step toward this: Developing a unified vision of the factory of the future.