RIMAC Technology
Industrialisierung von Fertigungs-, Montage- und Logistikprozessen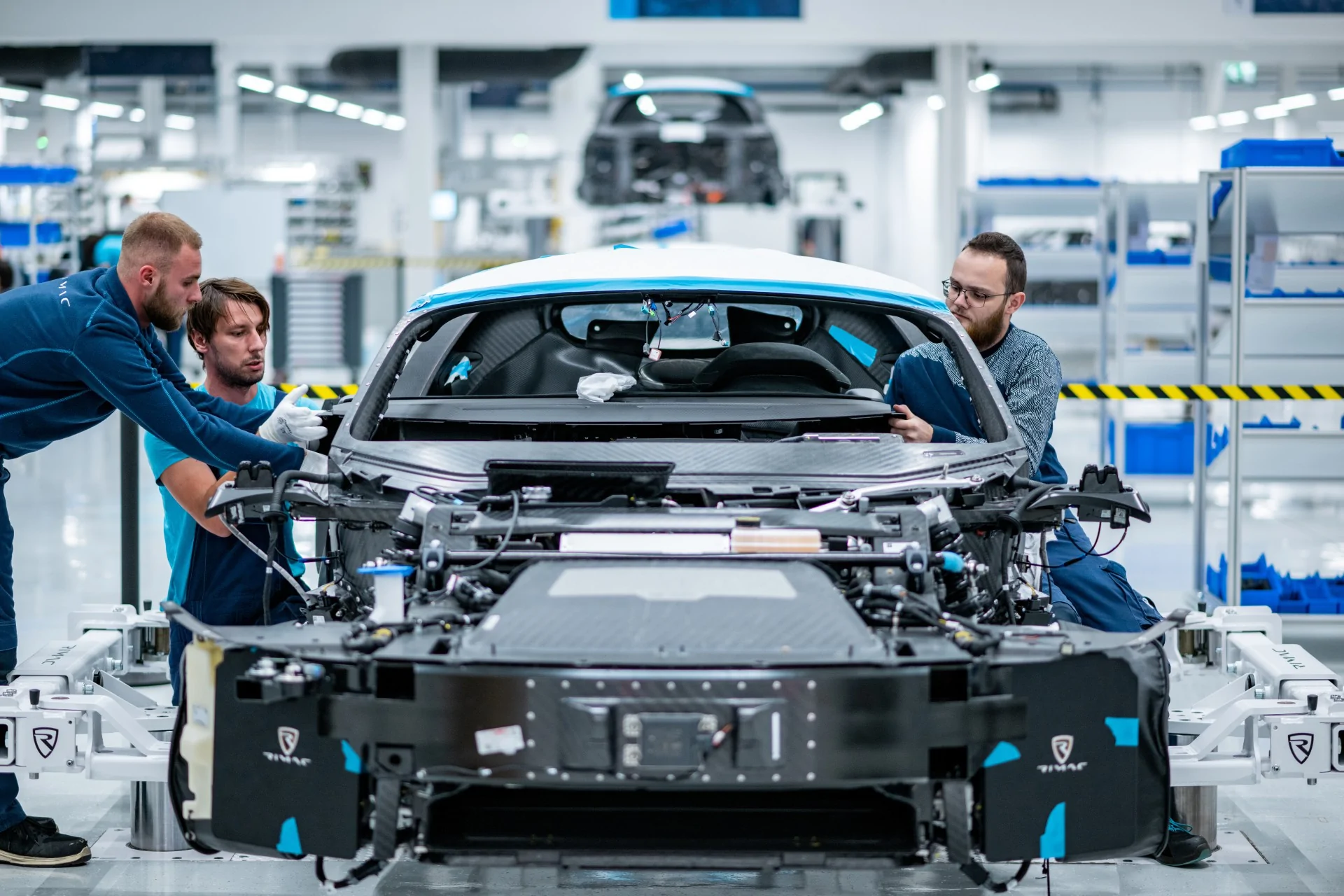
Projektansatz
Die Automobilindustrie ist die höchste Liga optimierter Prozesse. Um in dieser Branche wettbewerbsfähig zu sein, müssen sich Unternehmen durch Innovation und Technik auszeichnen - doch das alleine reicht nicht aus. Stattdessen müssen Unternehmen in der Lage sein, die globalen Märkte mit großen Mengen just-in-time zu bedienen und gleichzeitig höchste Produktqualität zu gewährleisten, insbesondere im schnell wachsenden Geschäft mit Elektrofahrzeugen und deren Antriebsstrangkomponenten. Dies erfordert ein Höchstmaß an Standardisierung und operativer Exzellenz in mehreren Disziplinen.
Als hochinnovatives, schnell wachsendes Unternehmen in der Elektroautobranche sah sich RIMAC mit genau diesen Herausforderungen konfrontiert, als es sich von einem technisch versierten Ingenieurbüro, das Einzelprototypen und Kleinserien herstellte, zur weltbesten Marke für Elektro-Hypercars entwickelte, die mehr als 150 der exklusivsten Hypercars und Tausende von Hochleistungskomponenten für den elektrischen Antriebsstrang liefert. Die Skalierung auf ein solches Niveau erfordert ein gründliches Design von hoch standardisierten Geschäfts- und Betriebsprozessen, einschließlich ihrer Implementierung in der Fertigung und in den zugrunde liegenden IT-Systemen.
NEONEX unterstützte RIMAC bei der Bewältigung dieser Herausforderung in einem 13-monatigen Projekt. Dabei haben RIMAC und NEONEX durch den Einsatz modernster Technologie schrittweise Prozesse der operativen Exzellenz geschaffen. In unserer Geschichte können Sie die Details erfahren und sich für Ihre eigene Reise auf die nächste Stufe der professionellen Exzellenz und Produktivität inspirieren lassen.
Der Nutzen für RIMAC
Umgesetzte Use Cases
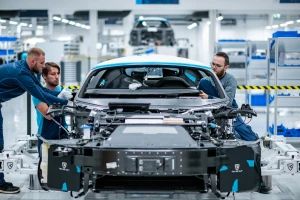
End-to-End-Geschäftsprozess-Definition
- End-to-End-Geschäftsprozessdesign
- ERP-Blueprinting
- ERP-Implementierung
RIMAC begann als ingenieurgetriebenes Hightech-Start-up, das die bemerkenswertesten Elektro-Hypercars und Elektrofahrzeugkomponenten herstellt. Da die Produktionsvolumina sowohl bei Autos als auch bei Technologieprodukten deutlich wachsen sollten, reichen hervorragende Leistungen in der Entwicklung aber nicht aus. Ein OEM und Tier-1-Zulieferer der Automobilindustrie muss seine Betriebsabläufe stattdessen auf hochgradig standardisierte und effiziente Weise beherrschen.
An dieser Stelle kommen ERP-Systeme ins Spiel. Sie helfen Unternehmen bei der Standardisierung und Skalierung ihrer End-to-End-Geschäftsprozesse auf ein professionelles Niveau, das es ihnen ermöglicht, qualitativ hochwertige Produkte in großem Umfang effizient herzustellen.
Gemeinsam mit dem Team von RIMAC und in enger Zusammenarbeit mit einem Systemintegrator entwarf NEONEX End-to-End Geschäftsprozesse, die in RIMACs neuem Infor LN ERP System implementiert werden sollten. Der Schlüssel zum Erfolg bei der Gestaltung von Geschäftsprozessen wie "Order-to-Cash", "Plan-to-Deliver" oder "Issue-to-Resolution" lag darin, eine Balance zwischen den in der Automobilindustrie existierenden Best-Practice-Standards und einem pragmatischen Ansatz bei der Gestaltung der einzelnen Prozessschritte zu finden, die der hohen Dynamik von RIMAC als Innovationsführer in seiner Branche entsprechen.
Das Ergebnis dieser Tätigkeit war eine Reihe von elf Business Blueprints als Grundlage für die gesamte ERP-Implementierung, die die RIMAC-Gruppe auf die nächste Stufe der Geschäftsprozess-Exzellenz hievte.
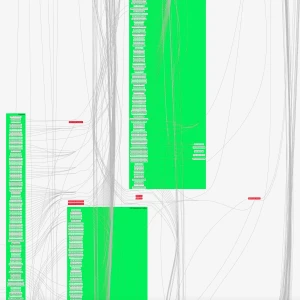
Datenbasiertes Design von Wertströmen und Produktionsprozessen
- Produktionsprozessdesign
- Datenbasiertes Wertstromdesign
Die Geschäftsprozesse eines Unternehmens zu beherrschen ist ein wichtiger Schritt - aber nicht ausreichend, um Spitzenleistungen zu erzielen. Um in der ersten Liga der Automobilunternehmen mitzuspielen, bedarf es vielmehr perfekt gestalteter Fertigungs- und Montageprozesse, die optimal in ERP-Regelkreise integriert sind.
Um die bestmögliche Gestaltung aller Prozesse, die den Wertstrom von RIMAC ausmachen, zu erreichen, wandte NEONEX sein datenbasiertes Wertstromdesign (deepVSD) an. Diese Methode wurde von NEONEX entwickelt und ermöglicht die Gestaltung von Up- und Downstream-Prozessen, die Identifizierung von Schrittmacherprozessen und Taktzeiten sowie die Berechnung von Supermarktgrößen und die Definition von Kanban-Zyklen für einen optimalen Materialfluss. Darüber hinaus betrachtet diese Methode das Wertstromdesign nicht nur ein oder zwei Hauptprodukte, wie es das klassische Wertstromdesign tut, sondern das gesamte Produktportfolio.
Basierend auf diesen Berechnungen wurden Steuerungsprinzipien für die RIMAC-Prozesse im ERP-System abgeleitet und entsprechende Stammdaten erstellt, um diese Prozesse nicht nur auf konzeptioneller, sondern auch auf IT-technischer Ebene umzusetzen.
Das Ergebnis dieser Initiative ist ein auf OEE und Kapazitätsannahmen basierender Wertstrom, der die verschiedenen Produktionsbereiche von der Endmontagelinie entkoppelt. Dadurch werden die Durchlaufzeiten durch die Einrichtung eines kontinuierlichen Materialflusses erheblich reduziert. Darüber hinaus wurden feinkörnige Materialflüsse, Nachschubzyklen, Arbeitspläne und Steuerungsprinzipien entwickelt und im ERP-System für sechs verschiedene Abteilungen von RIMAC implementiert.
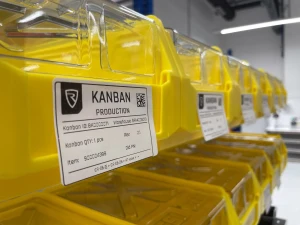
Logistikkonzeptentwicklung und Kalkulation
- Lagerkalkulation
- Milkrun Design
- Plan für jedes Teil Definition der Transportklassen
Um die Operations in einen Fluss zu bringen, reicht es nicht aus, Fertigungs- und Montageprozesse zu gestalten. Vielmehr muss die Logistik dafür sorgen, dass jede Maschine und jeder Arbeitsplatz in einer Fabrik zuverlässig mit Material versorgt wird.
Der Entwurf eines Logistiksystems für die Produktion von RIMAC umfasste daher die Einrichtung der Lagerstruktur pro Produktionsstandort und pro juristischer Einheit einschließlich einer Berechnung der erforderlichen Abmessungen. Für die Versorgung der Produktion mit Material aus Lagern und Supermärkten wurden Milkrun-Systeme konzipiert und berechnet. Darüber hinaus wurden die Versorgungsstufen von großen Lagern bis hin zu einzelnen Kanban-Regalen sowie die Transportklassen für jedes umzuschlagende Material in feiner Granularität definiert.
Das Ergebnis dieser Tätigkeit sind Logistikprozesse, die nicht nur perfekt mit den geplanten Fertigungs- und Montageprozessen integriert sind, sondern auch die spezifischen Anforderungen der Anlagenstruktur und -technik berücksichtigen. Darüber hinaus wurden relevante Stammdaten erstellt, um die geplante Struktur (z. B. Anzahl und Lage der Lager und Supermärkte, Milchstraßen und Haltepunkte usw.) sowie die physischen Eigenschaften der erstellten Logistikprozesse (z. B. Anzahl der Lagerplätze, verwendete Transportbehälter für bestimmte Materialien usw.) im ERP-System abzubilden.
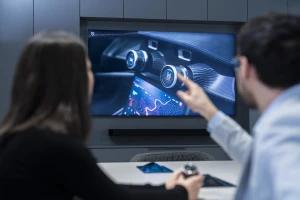
Schnittstellendefinition von ERP zu C2 Vertriebskonfigurator
- Vertriebskonfigurator
- ERP-Produktkonfigurator
Die Konfiguration eines Autos ist ein komplexer Prozess, vor allem, wenn es sich um ein so exklusives Hypercar wie den RIMAC NEVERA handelt, bei dem zahlreiche Individualisierungskombinationen zur Auswahl stehen. Automobilhersteller bieten in der Regel Produktkonfiguratoren an, die den Kunden helfen, die richtigen Optionen und Pakete für ihr Traumauto zu finden. Das Ergebnis einer solchen Konfiguration ist in der Regel eine Ausstattungsliste und ein Designentwurf für das konfigurierte Auto.
An diesem Punkt kommt das ERP-System ins Spiel, das die Merkmalliste in eine Stückliste übersetzen muss, um das konfigurierte Fahrzeug zu produzieren. Das bedeutet, dass die Optionscodes der Ausstattungspakete und Designpakete mit den ERP-Positionscodes für alle benötigten Materialien abgeglichen werden müssen. In einem zweiten Schritt werden dann mit Hilfe des ERP-Systems die genauen Fertigungs- und Montageschritte geplant, die auszuführen sind, bis das Endprodukt vom Band laufen kann.
Gemeinsam mit dem RIMAC-Engineering-, Sales- und Operations-Team gestaltete NEONEX die Stücklistenstruktur für die RIMAC NEVERA innerhalb des ERP-Systems, um Varianten- und Konfigurationsmöglichkeiten optimal abzubilden. Darüber hinaus wurde eine genaue Prozesslandkarte erstellt. Diese zeigt, wie die Konfiguration eines RIMAC NEVERA-Hypercars im ERP-System Infor LN gemeinsam mit den Spezialisten des Systemintegrators in eine zu bauende Struktur übersetzt wird.
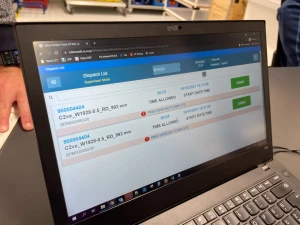
Überprüfung der Implementierung von Produktionskontrollprozessen im ERP-System
- ERP-Prüfung
- ERP-Prüfverfahren
Die Definition eines detaillierten Wertstroms für jede einzelne Werkstatt in der Produktion ist ein erster wichtiger Schritt bei der Skalierung von Produktionsprozessen. Es ist jedoch von entscheidender Bedeutung zu überprüfen, ob die entworfenen Konzepte auch wirklich im ERP-System umgesetzt wurden. Daher ist das Testen ein wesentlicher Bestandteil eines jeden ERP-Einführungsprojekts. In der Regel werden eine Vielzahl von Einheitstests und Integrationstests durchgeführt, um sicherzustellen, dass jeder Geschäftsprozess korrekt funktioniert, wenn der Schlüssel gedreht wird, um die Produktion mit einem neuen ERP-System zu starten.
In dem Projekt mit RIMAC hat NEONEX die im ERP-System realisierten Produktionssteuerungsprozesse eingehend getestet. Dabei wurde geprüft, ob Produktionsaufträge erfolgreich an das System freigegeben werden können, ob die zugehörigen Dokumente korrekt erzeugt werden können, ob die produzierte Materialmenge als "fertig" an das System gemeldet werden kann und ob ein Produktionsauftrag erfolgreich abgeschlossen werden kann, um den nächsten Schritt im Wertstrom auszulösen. In engem Zusammenhang mit dieser Funktionalität wurden alle entworfenen Kanban-Zyklen zur Steuerung des Materialnachschubs an den Arbeitsplätzen im Detail überprüft.
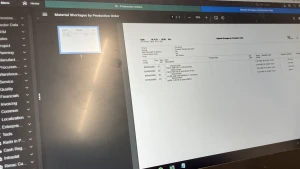
ERP-Cut-Over-Taskforce für den Betrieb
- Cut-Over Phase
- ERP Cut-Over
- Cut-Over Task-Force
Die Cut-over-Phase bei der Einführung eines ERP-Systems beschreibt einen sehr detaillierten Prozess des Abschaltens des bestehenden ERP-Systems und des Einschaltens der neuen ERP-Lösung.
Die Herausforderung in dieser Phase besteht darin, sicherzustellen, dass die Zeit, in der beide Systeme offline sind, minimiert wird und dass Bewegungs- und Transaktionsdaten, z. B. von durchgeführten Fertigungsaufträgen, Transportaufträgen oder gelieferten Materialien an das Lager und die Fertigung, nach der Aktivierung korrekt im neuen ERP-System gebucht werden. Diese Phase ist entscheidend für die erfolgreiche Implementierung, da sonst der aktuelle Betriebszustand eines Unternehmens nicht korrekt im neuen ERP-System wiedergegeben wird und der Abschluss eines Monats oder eines Geschäftsjahres nicht möglich ist.
NEONEX-Berater arbeiteten als Taskforce, um die RIMAC-Betriebsmitarbeiter bei der Durchführung des Cut-Overs operativ zu unterstützen. Dazu gehörte das Management von Aktivitäten wie die Generierung fehlender Einkaufs-, Fertigungs- und Transportaufträge, die Durchführung von Umlagerungen und die physische Neuetikettierung von Lagerstandorten. in hoher Frequenz.
Das Ergebnis dieser Initiative war eine gut überwachte Durchführung der mit der Umstellung verbundenen Aktivitäten, die den Weg für einen reibungslosen Übergang vom bestehenden Altsystem zur neuen ERP-Lösung ebnete.
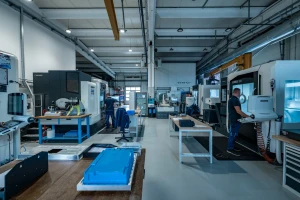
ERP-Implementierung mit agilem Projektmanagement
- Agiles Projektmanagement
ERP-Implementierungsprojekte werden in der Regel nach einer Wasserfalllogik durchgeführt. Ausgehend von einer Anfangsphase, in der die Anforderungen auf hoher Ebene bestätigt werden, gehen die Projekte in die Ausarbeitungsphase und die Erstellung von Business Blueprints über, in denen die realisierten Geschäftsprozesse und die damit verbundenen Funktionalitäten näher definiert werden. In der Aufbauphase werden mehrere Instanzen des ERP-Systems eingerichtet und die Tests beginnen. Die Schulung von Key- und End-Usern sowie die Migration von Stammdaten sind Aktivitäten zur Vorbereitung der Übergangsphase von einem bestehenden System zu einem neuen ERP während des Cut-Overs. Leistungsverbesserungen und Verfeinerungen der implementierten Funktionalitäten sind typische Post-Go-Live-Aktivitäten einer Optimierungs- oder Hypercare-Phase.
Ausgehend von diesem "idealen Welt"-Szenario stellt sich die Frage, wie ein groß angelegtes ERP-Projekt in einer komplexeren und dynamischen Start-up-Umgebung durchgeführt werden kann. Der Umgang mit neuen Mitarbeitern, sich ändernden Prioritäten, angepassten Prozessen oder strukturellen und rechtlichen Aspekten, die sich aus der Aufteilung von Unternehmen ergeben, erfordert die Fähigkeit, schnell zu reagieren, wenn die Dinge aus dem Ruder laufen könnten. Dies gilt insbesondere dann, wenn parallel dazu eine Pandemie für weitere Unsicherheiten sorgt.
Daher haben NEONEX und RIMAC einen agilen Ansatz angewandt, der drei Schlüsselelemente umfasst. Erstens wurde ein kurzzyklischer Sprint-Rahmen mit wöchentlichen Planungs- und Überprüfungsmeetings eingerichtet, um für Struktur zu sorgen und die Möglichkeit zu haben, innerhalb kurzer Zeit auf Abweichungen zu reagieren. Zweitens wurden interdisziplinäre Teams gebildet, die mit einem hohen Maß an Autonomie an bestimmten Themen arbeiteten und die erforderlichen Entscheidungen selbständig trafen, ohne sich in zu viele Entscheidungsschleifen begeben zu müssen. Schließlich wurden Fortschrittsverfolgung, Abweichungsmanagement und Priorisierung auf der Grundlage moderner agiler Werkzeuge wie Jira durchgeführt, um die bestmögliche Transparenz über geplante, aktive und abgeschlossene Aktivitäten zu gewährleisten.
Das Ergebnis dieses Ansatzes war, dass trotz der gegebenen Komplexität und Umstände konstante Fortschritte erzielt und die Projektziele erreicht wurden. Das ERP-System hob RIMAC auf die nächste Stufe eines führenden Unternehmens für große EV-Komponenten und eines hochexklusiven Hypercar-Herstellers.